Burger King #3032 - S St
417 S St, Eureka
Monday, Aug. 2, 2021 (3 violations)
Routine Inspection
36. Equipment / Utensils approved; installed, clean, good repair, capacity.
Conditions Observed: Observed mold like substance on interior of ice machine. Follow manufacturer’s instructions for cleaning and sanitizing the ice machine to prevent mold growth. Observed back panel of soft-serve machine is not secured to the unit. Repair/replace back panel of soft-serve machine to prevent potential harborage location for vermin.
ROACHY SAYS:
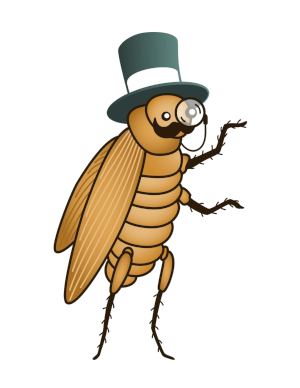
“Utensils and equipment shall be kept fully operative and in good repair. All new and replacement equipment shall be properly installed and be certified or classified for sanitation by an ANSI accredited certification program. Electrical appliances must meet UL standards. Single-use articles shall not allow migration of deleterious substances or impart colors, odors, or tastes to food. Multi-use food contact surfaces must be smooth, free of breaks, chips, and similar imperfections; free of sharp internal angles, corners, and crevices; finished to have smooth welds and joints; be accessible for cleaning and inspection. Unless specified, wood and wood wicker may not be used as a food-contact surface. Unless specified, copper and copper alloys such as brass may not be used in contact with a food that has a pH below six or for a fitting between a backflow preventer and a carbonator. Beverage tubing and cold-plate beverage cooling devices cannot be installed in contact with stored ice intended to be used as food. Equipment that is not movable must be installed to allow for cleaning in place. Cutting or piercing parts of can openers must be readily removable. Facilities that wash, rinse, soak, thaw, or similarly prepare foods shall be provided with a approved food preparation sink. Reservoirs that supply water to produce foggers must be cleaned and maintained. Surfaces such as cutting blocks and boards that are subject to scratching and scoring shall be resurfaced or replaced if they can no longer be effectively cleaned and sanitized. (114130, 114130.1, 114130.2, 114130.3, 114130.4, 114130.5, 114130.6, 114132, 114133, 114137, 114139, 114153, 114163, 114165, 114167, 114169, 114175, 114177, 114180, 114182)”
42. Garbage and refuse properly disposed; facilities maintained.
Conditions Observed: Observed boxes and debris on ground surrounding garbage dumpster. Observed dumpster gate unlocked and open over the duration of the inspection. Maintain garbage facilities clean; recommend keeping gate locked at all times to prevent passage or entrance of people and/or animals.
ROACHY SAYS:
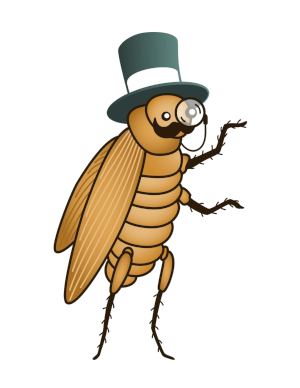
“The exterior premises of a food facility shall be kept free of litter and rubbish. All food waste and rubbish shall be kept in nonabsorbent, durable, cleanable, leak-proof, and rodent-proof containers. Containers shall have close-fitting lids and be covered at all times. All waste must be removed and disposed of as frequently as necessary to prevent the development of objectionable odors and other conditions that attract or harbor insects or rodents. (114244, 114245, 114245.1, 114245.2, 114245.3, 114245.4, 114245.5, 114245.6, 114245.7)”
45. Floor, walls, and ceilings: built, maintained, clean.
Conditions Observed: Observed food debris on floors under and behind equipment. Observed food debris in floor sink baskets. Maintain floors clean and free of debris to prevent buildup or potential food source for vermin.
ROACHY SAYS:
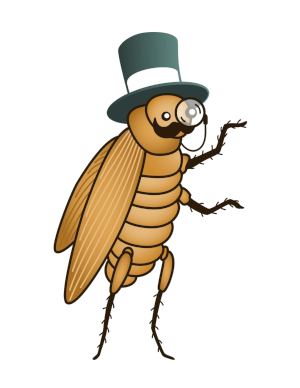
“Food facilities shall be fully enclosed in a building consisting of permanent floors, walls, and an overhead structure that meets minimum standards. The walls and ceiling shall be smooth, durable, nonabsorbent, and easily cleanable. Flooring and base coving shall be smooth, durable, and made of approved nonabsorbent material that is easily cleanable. Floor surfaces shall be coved at the juncture of the floor and wall with a 3/8 inch minimum radius and shall extend up the wall at least 4 inches. (114143(d), 114266, 114268, 114268.1, 114271, 114272)”
Tuesday, March 2, 2021 (0 violations)
Routine Inspection
ROACHY SAYS:
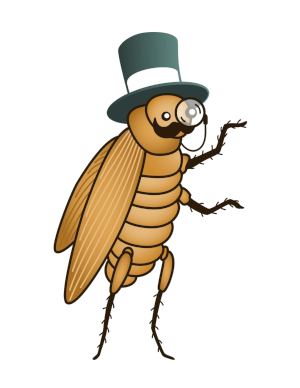
“Take a victory lap, Burger King #3032 - S St! In the race that is maintaining a clean and healthy establishment you've earned Roachy's gold medal! Eat here today, everyone!!”
Thursday, Oct. 29, 2020 (0 violations)
Routine Inspection
ROACHY SAYS:
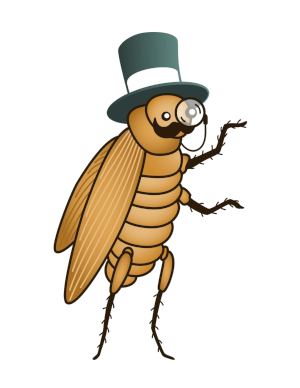
“Huzzah! This establishment has successfully impressed the government! Kudos, Burger King #3032 - S St!!”
Friday, July 10, 2020 (2 violations)
Routine Inspection
22. Hot and Cold Water Available
Conditions Observed: Hot water at 3-compartment warewash sink was measured at 116° F. Hot water shall be supplied at a minimum temperature of at least 120° F measured from the faucet. Please adjust/repair to ensure hot water temperature at faucet reaches at least 120° F.
ROACHY SAYS:
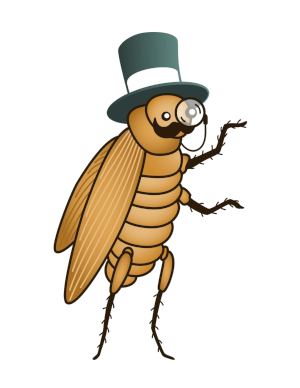
“An adequate, protected, pressurized, approved potable supply of hot and cold water shall be provided at all times. Hot water shall be supplied at a minimum temperature of 120F when measured from the faucet. The temperature of water provided to handwashing facilities shall be at least 100F. Handwashing facilities equipped with non-adjustable faucets shall have their temperature set between 100F and 108F. Hot water shall be provided at the food preparation sink and janitorial sink. (113953(c), 114099.2(b), 114163(a)(3), 114189, 114192, 114192.1, 114195)”
34. Non-food-contact surfaces clean.
Conditions Observed: Accumulation of spills/debris was observed on inside bottom of under-counter cabinet where cleaning supplies are stored (behind grill). All non-food contact surfaces must be maintained clean. Please clean this area in order to avoid the potential for attracting vermin.
ROACHY SAYS:
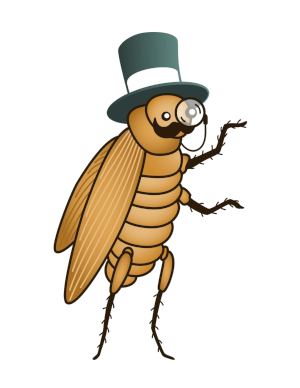
“Nonfood-contact surfaces of equipment shall be kept free of an accumulation of dust, dirt, food residue, and other debris. (114115(b))”
Wednesday, Feb. 19, 2020 (6 violations)
Routine Inspection
06. Hands clean and properly washed; gloves used properly.
Conditions Observed: Employees observed handling tongs and bags in contact with raw frozen burger patties and changing tasks to work with ready-to-eat foods without changing gloves and proper handwashing. Discussed with employees on site during inspection; corrected on site; thank you. Please ensure that all employees are trained on the importance of proper handwashing and glove change practices before changing tasks after handling any raw foods in order to prevent cross-contamination.
ROACHY SAYS:
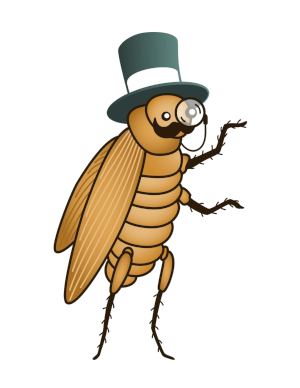
“Food employees shall minimize bare hand and arm contact with nonprepackaged food that is in ready to eat form. Whenever gloves are worn, they shall be changed, replaced, or washed as often as handwashing is required. Single-use gloves shall not be washed. Employees shall wash their hands in the following situations: immediately before engaging in food preparation including working with nonprepackaged food, clean equipment and utensils and unwrapped single-use food containers and utensils; after touching bare human body parts other than clean hands and clean exposed portions of arms; after using the toilet room; after caring for or handling any animal; after coughing, sneezing, using a handkerchief or disposable tissue, using tobacco, eating or drinking; after handling soiled equipment or utensils; during food preparation, as often as necessary to remove soil and contamination and to prevent cross-contamination when changing tasks; when switching from working with raw food and working with ready-to-eat foods; before initially donning gloves for working with food; before dispensing or serving food handling clean tableware and serving utensils in the food service area; after engaging in other activities that contaminate the hands. (113952, 113953.3, 113953.4, 113961, 113968, 113973)”
11. Proper cooking time and temperatures.
Conditions Observed: Cooked burgers direct from grill (right side) measured below required minimum internal temperature of 155° F (136° F and 148° F). Burgers on left side of grill were measured at correct temperature (159 ° F). Corrected on site; cooked burgers from left side of grill were discarded and equipment adjusted. Cooked burger after adjustment measured at 161.1° F. COS. Discussion with staff and manager confirme that cooking temps are checked throughout the day but that daily cleaning/maintenance had been performed on the grill after this morning’s temperature check. Please monitor and re-check temperatures after any cleaning or adjustments to ensure that the grill is still cooking burgers to required minimum internal temperatures.
ROACHY SAYS:
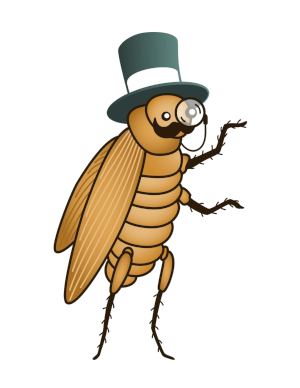
“Fruits and vegetables that are cooked for hot holding shall be cooked to a minimum temperature of 135F. Single pieces of meat, fish, and raw shell eggs for immediate service, shall be heated to an internal temperature of 145F for 15 seconds. Comminuted meat, injected meat, raw eggs not for immediate service, or any food containing comminuted meat or raw eggs, shall be heated to an internal temperature of 155F for 15 seconds. Poultry, comminuted poultry, stuffed fish, stuffed meat, and stuffed poultry shall be heated to an internal temperature of 165F for 15 seconds. Other temperature requirements may apply. (114004, 114008, 114010)”
34. Non-food-contact surfaces clean.
Conditions Observed: There was heavy buildup of grease and food debris observed behind the burger grill. Heavy accumulation of spills and food debris were observed inside the cabinets under the prep top, where bins of ready to eat foods are stored. Buildup also observed on customer self-service soda machine and in cabinets under soda machine. Soda lids in an opened package were touching dirty cabinet surface. Floor drains in kitchen area were unclean and contained food debris. Accumulations of dirt and food debris were also observed on most non-food-contact surfaces throughout the facility. Please thoroughly clean all equipment and non-food contact surfaces throughout the facility and maintain clean.
ROACHY SAYS:
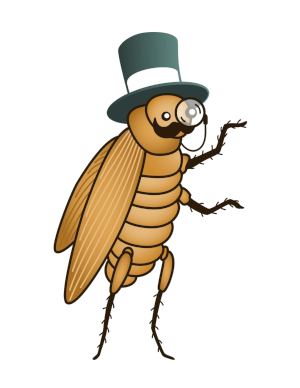
“Nonfood-contact surfaces of equipment shall be kept free of an accumulation of dust, dirt, food residue, and other debris. (114115(b))”
36. Equipment / Utensils approved; installed, clean, good repair, capacity.
Conditions Observed: Gasket was missing from parts of walk-in freezer door. Light switch box next to freezer door was broken. Please repace gasket and light switch box and maintain all equipment in good repair.
ROACHY SAYS:
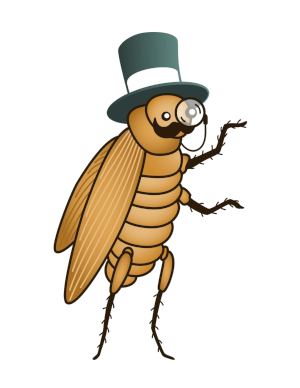
“Utensils and equipment shall be kept fully operative and in good repair. All new and replacement equipment shall be properly installed and be certified or classified for sanitation by an ANSI accredited certification program. Electrical appliances must meet UL standards. Single-use articles shall not allow migration of deleterious substances or impart colors, odors, or tastes to food. Multi-use food contact surfaces must be smooth, free of breaks, chips, and similar imperfections; free of sharp internal angles, corners, and crevices; finished to have smooth welds and joints; be accessible for cleaning and inspection. Unless specified, wood and wood wicker may not be used as a food-contact surface. Unless specified, copper and copper alloys such as brass may not be used in contact with a food that has a pH below six or for a fitting between a backflow preventer and a carbonator. Beverage tubing and cold-plate beverage cooling devices cannot be installed in contact with stored ice intended to be used as food. Equipment that is not movable must be installed to allow for cleaning in place. Cutting or piercing parts of can openers must be readily removable. Facilities that wash, rinse, soak, thaw, or similarly prepare foods shall be provided with a approved food preparation sink. Reservoirs that supply water to produce foggers must be cleaned and maintained. Surfaces such as cutting blocks and boards that are subject to scratching and scoring shall be resurfaced or replaced if they can no longer be effectively cleaned and sanitized. (114130, 114130.1, 114130.2, 114130.3, 114130.4, 114130.5, 114130.6, 114132, 114133, 114137, 114139, 114153, 114163, 114165, 114167, 114169, 114175, 114177, 114180, 114182)”
41. Plumbing: proper backflow devices.
Conditions Observed: Pipe associated with fire suppression system was dripping onto floor near mop sink in janitorial room. Faucets and sprayer at 3-compartment warewash sink were leaking. Hose at “t” junction behind CO2 tank had a leak. No backflow device was observed between the CO2 tank lines and copper pipes leading to water supply and ice machine. Pipe/hose was leaking behind trash compactor in garbage enclosure. Please repair all plumbing leaks. Please ensure that a backflow device is installed to prevent backflow of carbonated water which could corrode copper pipes.
ROACHY SAYS:
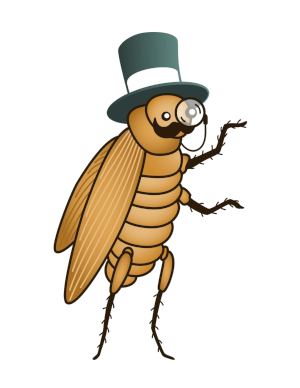
“Steam tables, ice machines, ice bins, food preparation sinks, display cases, walk-in refrigeration units, and other similar equipment that discharge liquid waste shall drain into a floor sink with an air gap or other approved type of receptor. All plumbing and plumbing fixtures shall be installed in compliance with applicable local plumbing ordinances, maintained so as to prevent any contamination, kept clean, fully operative, and in good repair. The potable water supply shall be protected with a backflow or back siphonage protection device. Any hose used for potable water shall be of approved materials, labeled, properly stored, and used for no other purpose. Liquid drain lines shall not pass through an ice machine or an ice storage bin. (114171, 114190, 114192, 114193, 114193.1, 114199, 114201, 114269)”
45. Floor, walls, and ceilings: built, maintained, clean.
Conditions Observed: Floors throughout the facility had accumulations of grease, grime, and food and other debris. Walls throughout the facility had accumulations of food debris. Walls behind handwash sink and near janitorial/mop sink had holes. Coving/tile at junction of floor and wall near mop sink was damaged. Please repair floor coving and gaps in walls in order to prevent ingress of vermin. Please thoroughly clean all floors and walls and maintain clean.
ROACHY SAYS:
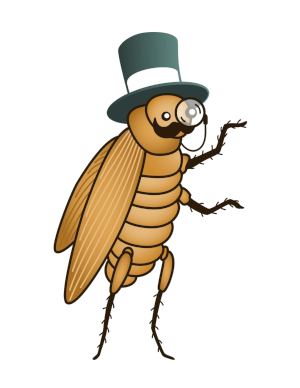
“Food facilities shall be fully enclosed in a building consisting of permanent floors, walls, and an overhead structure that meets minimum standards. The walls and ceiling shall be smooth, durable, nonabsorbent, and easily cleanable. Flooring and base coving shall be smooth, durable, and made of approved nonabsorbent material that is easily cleanable. Floor surfaces shall be coved at the juncture of the floor and wall with a 3/8 inch minimum radius and shall extend up the wall at least 4 inches. (114143(d), 114266, 114268, 114268.1, 114271, 114272)”
Tuesday, July 23, 2019 (7 violations)
Routine Inspection
07. Adequate handwash facilities supplied and accessible.
Conditions Observed: Observed unclean handwash sink. The handwash sink shall remain clean and unobstructed at all times for proper handwashing. Observed 2 rolls of paper towels sitting out of a dispenser in 2 locations in the kitchen. Paper towels shall be stocked in dispensers to prevent contamination. If employees are using paper towels to wipe their hands, this practice must immediately stop; Instruct all employees to properly handwash in the designated handwash sink when hands become soiled/contaminated.
ROACHY SAYS:
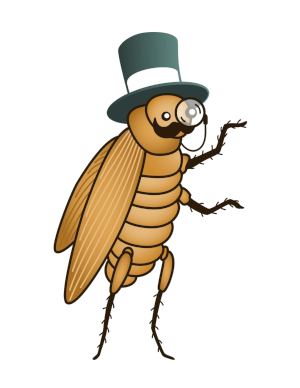
“Handwashing facilities shall be provided within or adjacent to toilet rooms, food preparation, and warewashing areas. Handwashing facilities shall be clean, unobstructed, and accessible at all times. Handwashing facilities shall be provided with soap and sanitary single use towels in approved dispensers. Dispensers shall be maintained in good repair. A handwashing facility shall not be used for purposes other than handwashing. (113953, 113953.1, 113953.2, 114067(f))”
09. Time as public health control; procedures and records.
Conditions Observed: Observed 2 unlabeled dessert sauces held out of temperature control. All foods included on the “Fresh & Ready Product Holding System Chart” shall be time labeled accordingly (carmel topping - 21 days). 2 unlabeled sauces were discarded. This repeat major violation was corrected on site.
ROACHY SAYS:
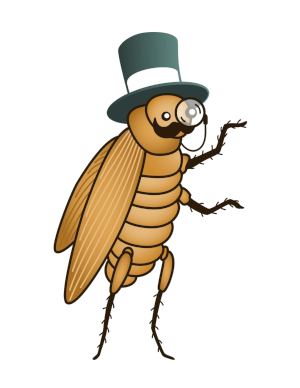
“When time as a public health control is used, the following procedures shall be observed: food items shall be marked to indicate four hours past the time when the food was removed from temperature control, food shall be served or discarded within the four hour time limit. Written procedures shall be maintained in the food facility and made available to the enforcement agency upon request, that ensure compliance with this section and section 114002, for food that is prepared, cooked, and refrigerated before time is used as a public health control. Time only may not be used in Licensed health care facilities, public school cafeterias, or private school cafeterias. (114000)”
31. Food storage; food storage containers identified.
Conditions Observed: Observed onions in direct contact with the floor. Store all foods at least 6 inches above the floor to prevent contamination and potential vermin attraction.
ROACHY SAYS:
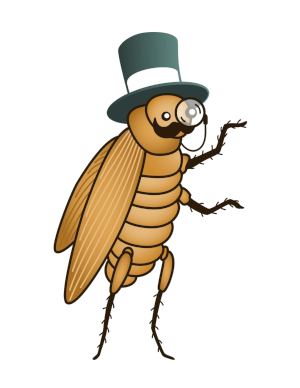
“Adequate and suitable space shall be provided for the storage of food. Food shall be protected from contamination by storing the food in a clean, dry location, where it is not exposed to splash, dust, vermin, or other forms of contamination or adulteration, and at least six inches above the floor. Food shall not be stored in any of the following ways: in locker rooms, toilet rooms, dressing rooms, refuse rooms, mechanical rooms, under sewer lines that are not shielded to intercept potential drips, under leaking water lines, including leaking automatic fire sprinklers heads, or under lines on which water has condensated, under open stairwells or under sources of contamination. Working containers holding food or food ingredients that are removed from their original packages for use in the food facility shall be identified with the common name of the food. Non-prepackaged food may not be stored in direct contact with undrained ice. Products that are held by the permit holder for credit, redemption, or return to the distributor, such as damaged, spoiled, or recalled products shall be segregated and held in designated areas that are separated from food, equipment, utensils, linens, and single-use articles. (114047, 141049, 114051, 114053, 114055, 114067(h), 114069(b))”
34. Non-food-contact surfaces clean.
Conditions Observed: Observed food debris and/or grease accumulation on interior and exterior non-food contact surfaces of all equipment, including but not limited to, refrigerators, freezers, floor sinks, soda machines, ice cream machine, blender, cabinets, shelves, etc. Clean non-food contact surfaces regularly to prevent buildup and possible vermin attraction.
ROACHY SAYS:
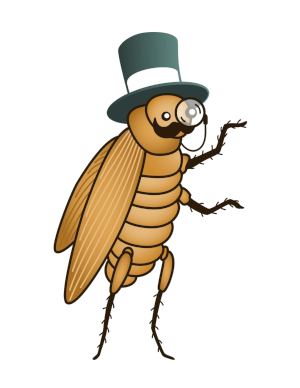
“Nonfood-contact surfaces of equipment shall be kept free of an accumulation of dust, dirt, food residue, and other debris. (114115(b))”
42. Garbage and refuse properly disposed; facilities maintained.
Conditions Observed: Observed debris on ground surrounding dumpster. Maintain dumpster area clean and free of debris.
ROACHY SAYS:
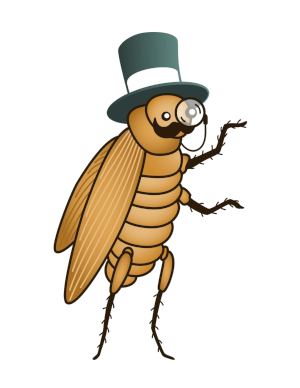
“The exterior premises of a food facility shall be kept free of litter and rubbish. All food waste and rubbish shall be kept in nonabsorbent, durable, cleanable, leak-proof, and rodent-proof containers. Containers shall have close-fitting lids and be covered at all times. All waste must be removed and disposed of as frequently as necessary to prevent the development of objectionable odors and other conditions that attract or harbor insects or rodents. (114244, 114245, 114245.1, 114245.2, 114245.3, 114245.4, 114245.5, 114245.6, 114245.7)”
44. Premises; personal/cleaning items; vermin-proofing.
Conditions Observed: Observed melted electrical cord behind rolling rack on North facing wall in the kitchen. Repair. Observed tall, thick hedges around the parameter of the facility providing harborage for the transient population. Recommend removing the hedges to visibly monitor premises of facility and/or install a fence around parameter of facility. Observed trash and debris in surrounding foliage of facility. Maintain premises clean and free of debris.
ROACHY SAYS:
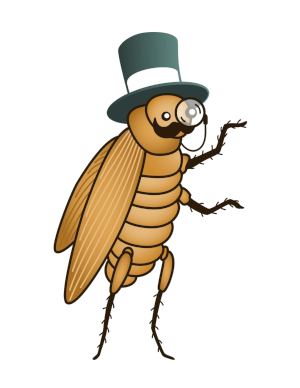
“All premises of a food facility shall be kept clean, fully operative, and in good repair. The premise of a food facility shall be free of litter and items unnecessary to the operation of the facility. Areas designated for employees to eat and drink shall be located so that food, clean equipent and utensils, linens, and single-use articles are protected from contamination. Personal items shall be stored in a designated area to prevent contamination of food or utensils. Food prep sinks, warewashing sinks, and handwashing sinks shall not be used for the cleaning or maintenance of tools or cleaning supplies or to dispose of mop water and similar liquid wastes. A dedicated janitorial sink with a drain shall be provided and conveniently located. A separate room, area, or cabinet shall be provided for cleaning supplies. The facility shall be kept vermin proof. Insect electrocution devices shall retain the insect within the device and shall not be located over food or utensil handling areas. (114123, 114143(a, b), 114256, 114256.1, 114256.2, 114256.4, 114257, 114257.1, 114259, 114259.2, 114259.3, 114279, 114281, 114282)”
45. Floor, walls, and ceilings: built, maintained, clean.
Conditions Observed: Observed failing coving adjacent to mop sink and under drive-thru window. Repair coving to provide a smooth, durable, nonabsorbent surface that is easy to clean. Observed soiled floors throughout facility, specifically under/behind equipment. Move equipment to clean floors regularly. Observed visibly soiled walls above/behind trash cans. Clean impacted areas regularly.
ROACHY SAYS:
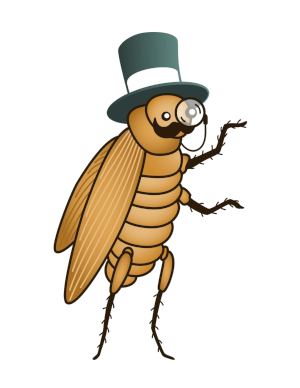
“Food facilities shall be fully enclosed in a building consisting of permanent floors, walls, and an overhead structure that meets minimum standards. The walls and ceiling shall be smooth, durable, nonabsorbent, and easily cleanable. Flooring and base coving shall be smooth, durable, and made of approved nonabsorbent material that is easily cleanable. Floor surfaces shall be coved at the juncture of the floor and wall with a 3/8 inch minimum radius and shall extend up the wall at least 4 inches. (114143(d), 114266, 114268, 114268.1, 114271, 114272)”
Monday, March 11, 2019 (5 violations)
Routine Inspection
09. Time as public health control; procedures and records.
Conditions Observed: Observed cooked bacon and chopped iceberg lettuce held out of temperature control, lacking time labels. Ensure employees are using time as a public health control and referring to “Fresh & Ready Product Holding System Chart” and time labeling potentially hazardous foods held out of temperature control accordingly (cooked bacon: 2 day hold; lettuce: 4 hours). Employee time labeled cooked bacon and iceberg lettuce. This major violation was corrected on site, thank you.
ROACHY SAYS:
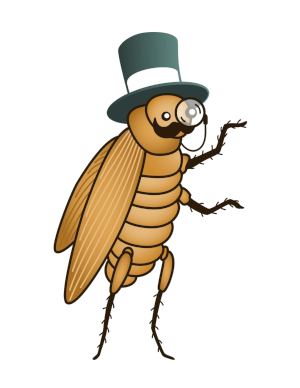
“When time as a public health control is used, the following procedures shall be observed: food items shall be marked to indicate four hours past the time when the food was removed from temperature control, food shall be served or discarded within the four hour time limit. Written procedures shall be maintained in the food facility and made available to the enforcement agency upon request, that ensure compliance with this section and section 114002, for food that is prepared, cooked, and refrigerated before time is used as a public health control. Time only may not be used in Licensed health care facilities, public school cafeterias, or private school cafeterias. (114000)”
28. Food separated and protected.
Conditions Observed: Observed uncovered bacon and chocolate chip cookies stored under ceiling fixtures containing dust accumulation. Cover all stored food to protect from contamination.
ROACHY SAYS:
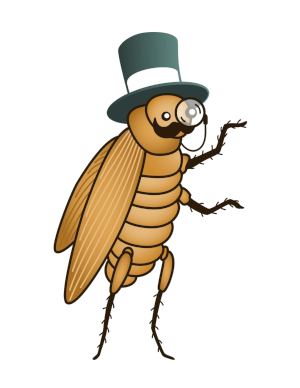
“Food shall be protected from contamination during transportation, storage, preparation, holding, and display. Adequate and suitable counter space shall be provided for all food preparation. Food preparation shall be conducted wthin an approved food compartment or fully enclosed food facility. Open-air barbecues shall be separated from public access. (113984(a-f), 113986, 114060, 114067(a,d,e,j), 114069(a, c, d), 114077, 114089.1(c), 114143(c,e))”
34. Non-food-contact surfaces clean.
Conditions Observed: Observed food debris inside small True prep table. Observed food debris and garbage in several floor sinks. Observed debris in cabinets under food assembly line. Observed sugar residue on both soda machines, ice cream machine, and Icee machine. Clean non-food contact surfaces of equipment regularly to prevent buildup and possible vermin attraction.
ROACHY SAYS:
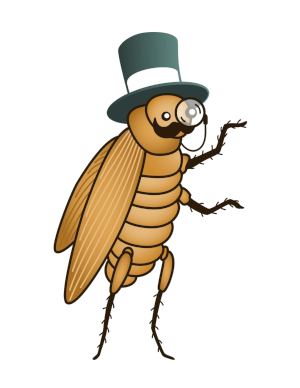
“Nonfood-contact surfaces of equipment shall be kept free of an accumulation of dust, dirt, food residue, and other debris. (114115(b))”
44. Premises; personal/cleaning items; vermin-proofing.
Conditions Observed: Observed container full of soda syrup in cabinet under drain board adjacent to soda machine in dining area. Remove container and repair leak, if applicable. Clean and sanitize area under cabinet to prevent vermin attraction. Observed unused True prep table in back of facility. Repair/replace/remove non-functioning True prep table. Observed tall, thick hedges of bushes around the parameter of the facility providing harborage for the transient population. Recommend removing hedges to visibly monitor premises of facility and/or install a fence around parameter of facility, as there is a hole in the hedges providing access from the vacant lot next door.
ROACHY SAYS:
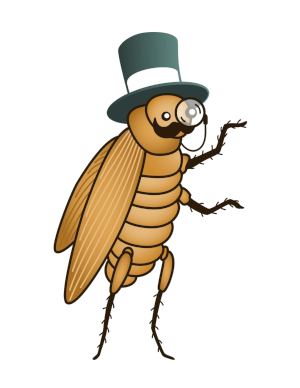
“All premises of a food facility shall be kept clean, fully operative, and in good repair. The premise of a food facility shall be free of litter and items unnecessary to the operation of the facility. Areas designated for employees to eat and drink shall be located so that food, clean equipent and utensils, linens, and single-use articles are protected from contamination. Personal items shall be stored in a designated area to prevent contamination of food or utensils. Food prep sinks, warewashing sinks, and handwashing sinks shall not be used for the cleaning or maintenance of tools or cleaning supplies or to dispose of mop water and similar liquid wastes. A dedicated janitorial sink with a drain shall be provided and conveniently located. A separate room, area, or cabinet shall be provided for cleaning supplies. The facility shall be kept vermin proof. Insect electrocution devices shall retain the insect within the device and shall not be located over food or utensil handling areas. (114123, 114143(a, b), 114256, 114256.1, 114256.2, 114256.4, 114257, 114257.1, 114259, 114259.2, 114259.3, 114279, 114281, 114282)”
45. Floor, walls, and ceilings: built, maintained, clean.
Conditions Observed: Observed failed coving adjacent to mop sink. Repair coving to provide a smooth, durable, nonabsorbent surface that is easy to clean. Observed visibly soiled floors throughout facility, specifically under/behind equipment. Move equipment to clean and sanitize floors regularly. Observed visibly soiled walls above/behind trash receptacles. Clean impacted area regularly to prevent buildup.
ROACHY SAYS:
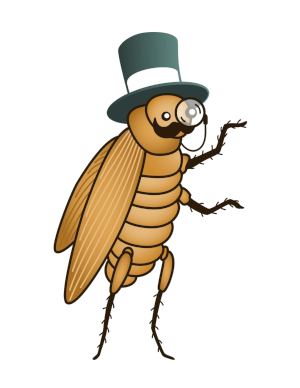
“Food facilities shall be fully enclosed in a building consisting of permanent floors, walls, and an overhead structure that meets minimum standards. The walls and ceiling shall be smooth, durable, nonabsorbent, and easily cleanable. Flooring and base coving shall be smooth, durable, and made of approved nonabsorbent material that is easily cleanable. Floor surfaces shall be coved at the juncture of the floor and wall with a 3/8 inch minimum radius and shall extend up the wall at least 4 inches. (114143(d), 114266, 114268, 114268.1, 114271, 114272)”