Nori Sushi & Steak
Salt Fish House
761 8th St A #, Arcata
Wednesday, Oct. 13, 2021 (6 violations)
Routine Inspection
01. Demonstration of knowledge.
Conditions Observed: Staff present at the inspection were initially unsure of how to measure the pH of the sushi rice. The pH probe and log were located. Inspector reviewed how to use the probe (calibration is required) and how to use test strips. Please be sure to have your sushi rice HACCP or standard operating procedure available for reference at all times. The persons preparing the sushi rice and/or rolling sushi must know how to measure the pH of the sushi rice and the correct pH.
ROACHY SAYS:
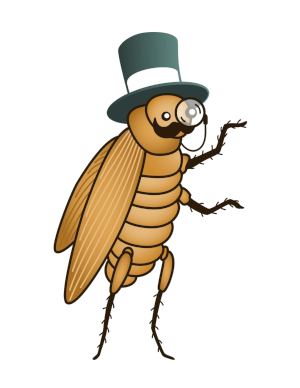
“The Person In Charge (PIC) and all employees shall have adequate knowledge and shall be properly trained in food safety as it relates to their assigned duties. The PIC shall have adequate knowledge of major food allergens, foods identified as major food allergens, and the symptoms that a major food allergen could cause. The PIC means a designated person who has knowledge of safe food handling practices and the major food allergens as they relate to the specific food preparation activities that occur at the food facility. (113947)”
17. Compliance with shell stock tags, condition, display.
Conditions Observed: No shell stock tag with the oysters in the 3-door fridge. As discussed during the inspection, keep the tag with the oysters until the stock is sold and then label and file.
ROACHY SAYS:
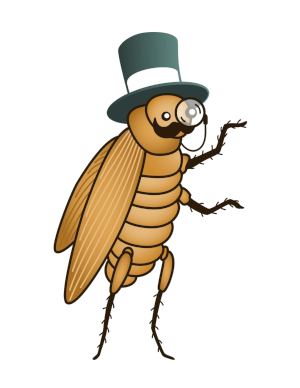
“Shellstock shall be obtained in containers that bear legible source identification tags. A food facility shall ensure that shellstock from one tagged or labeled container are not commingled with shellstock from another container with different certification numbers. Shellstock tags shall remain attached to the container that they are received in until the container is empty. The identity of the source of the shellstock sold or served shall be maintained for 90 days from the dates of harvest by using an approved recordkeeping system that keeps the tags or labels in chronological order correlated to the date or dates the shellstock is sold or served. The source of the shellstock on display shall be identified. Shellstock that are portioned or prepackaged shall have a copy of the corresponding shellstock tag. Except in accordance with an approved HACCP plan, molluscan shellfish life-support system display tanks shall not be used to display shellfish that are offered for human consumption. (114039-114039.5)”
27. Approved thawing methods used; frozen food.
Conditions Observed: Observed shrimp thawing in a bowl of standing water at food the prep sink. If thawing with water, water must be flowing/moving. See regulation description. Always thaw foods using an approved method.
ROACHY SAYS:
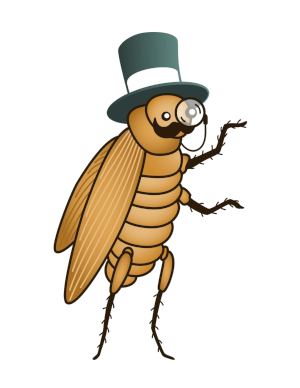
“Frozen foods shall be stored or displayed in their frozen state unless being thawed in the following manner: under refrigeration that maintains the food temperature at 41F or below, completely submerged under potable running water for a period not to exceed two hours at a water temperature of 70F or below and with sufficient water velocity to agitate and flush off loose particles into the sink drain, in a microwave oven if immediately followed by immediate preparation, or as part of a cooking process. (114018, 114020)”
31. Food storage; food storage containers identified.
Conditions Observed: Observed case of eggs above prepared spicy tuna; a few eggs had cracked. Store eggs below ready-to-eat foods. Review food storage order requirements with all kitchen staff.
ROACHY SAYS:
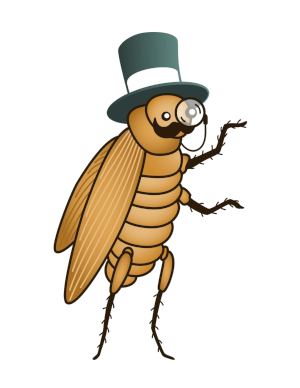
“Adequate and suitable space shall be provided for the storage of food. Food shall be protected from contamination by storing the food in a clean, dry location, where it is not exposed to splash, dust, vermin, or other forms of contamination or adulteration, and at least six inches above the floor. Food shall not be stored in any of the following ways: in locker rooms, toilet rooms, dressing rooms, refuse rooms, mechanical rooms, under sewer lines that are not shielded to intercept potential drips, under leaking water lines, including leaking automatic fire sprinklers heads, or under lines on which water has condensated, under open stairwells or under sources of contamination. Working containers holding food or food ingredients that are removed from their original packages for use in the food facility shall be identified with the common name of the food. Non-prepackaged food may not be stored in direct contact with undrained ice. Products that are held by the permit holder for credit, redemption, or return to the distributor, such as damaged, spoiled, or recalled products shall be segregated and held in designated areas that are separated from food, equipment, utensils, linens, and single-use articles. (114047, 141049, 114051, 114053, 114055, 114067(h), 114069(b))”
34. Non-food-contact surfaces clean.
Conditions Observed: Encountered an unpleasant malodor upon opening the dessert/produce fridge. Staff pulled items likely to be causing odor - thank you. As discussed during the inspection, maintain a tidy and organized fridge to prevent unpleasant odors.
ROACHY SAYS:
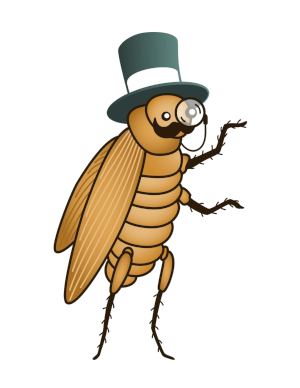
“Nonfood-contact surfaces of equipment shall be kept free of an accumulation of dust, dirt, food residue, and other debris. (114115(b))”
39. Thermometers provided and accurate.
Conditions Observed: Unable to locate thermometers in the kitchen prep fridges. Provide an NSF approved cold-holding thermometer for both fridges.
ROACHY SAYS:
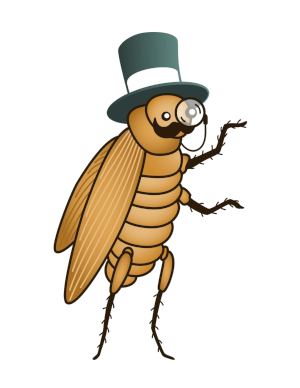
“An accurate easily readable metal probe thermometer suitable for measuring temperature of food shall be available to the food handler. Thermometers shall be calibrated in accordance with manufacturer's specifications as necessary to ensure their accuracy. A thermometer +/- 2 degrees F shall be provided for all refrigerators, hot and cold holding units, and high temperature warewashing machines. (114157, 114159)”
Wednesday, June 2, 2021 (1 violation)
Routine Inspection
24. No rodents, insects, birds, or animals.
Conditions Observed: Observed a cluster of 8 to 12 flies in front of the hostess station; observed a second cluster in the center of the kitchen. Increase pest control to remove flies from the facility. Maintain a vermin proof facility.
ROACHY SAYS:
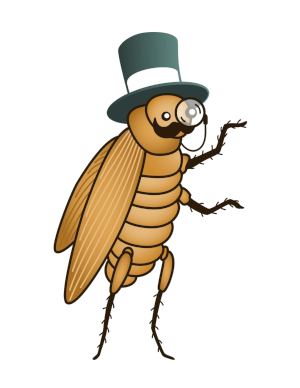
“A food facility shall be kept free of vermin. Live animals are prohibited from food facilities except as specified in 114259.5. Food facility employees shall not care for or handle animals that may be present in the food facility. Food facility employees are required to wash their hands after handling or caring for fish in an aquarium and/or shellfish, or crustacea, in display tanks and as specified in 114259.4. (114259.1, 114259.4, 114259.5)”
Friday, April 9, 2021 (0 violations)
CP - New Facility Inspection
ROACHY SAYS:
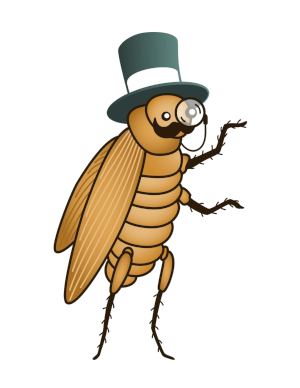
“Both patrons and the health department agree! This place sets the standard for Humboldt food facility cleanliness! All hail Nori Sushi & Steak!!”
Friday, June 5, 2020 (0 violations)
Routine Inspection
ROACHY SAYS:
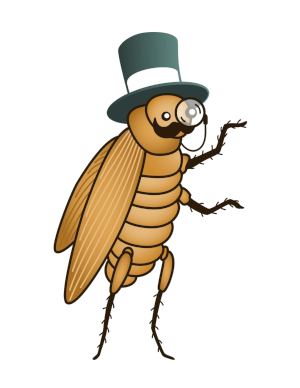
“Both patrons and the health department agree! This place sets the standard for Humboldt food facility cleanliness! All hail Nori Sushi & Steak!!”
Tuesday, Dec. 3, 2019 (5 violations)
Routine Inspection
08. Proper hot and cold holding temperatures.
Conditions Observed: Measured foods in the top right deli prep to be above 50 F (shredded cheese, 51 F; halved cabbage, 55 F). Employee obtain dividers, properly set up inserts, and closed lid. Keep food in direct contact with refrigeration. Measured cheese at the end of the inspection to be 46 F (cabbage was discarded).
ROACHY SAYS:
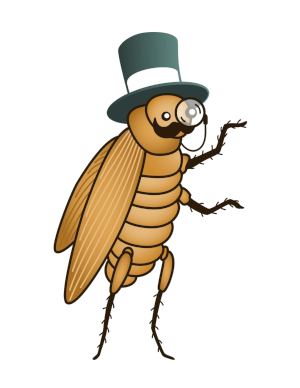
“Except during preparation, cooking, cooling, transportation to or from a retail food facility for a period of less than thirty minutes, when time is used as the public health control, or as otherwise specified, potentially hazardous foods shall be maintained at or below 41F or at or above 135F. The following foods may be held at or below 45F: raw shell eggs, unshucked live molluscan shellfish, pasteurized milk and pasteurized milk products in original sealed containers, potentially hazardous foods held during transportation. Potentially hazardous foods held for dispensing in serving lines and salad bars may be held at 45F, not to exceed 12 hours in a 24 hour period, if unused portions are discarded. Food preparation shall not exceed two cumulative hours without a return to the required holding temperatures. (113996, 113998, 114037, 114343(a))”
15. Food contact surfaces: clean and sanitized.
Conditions Observed: Observed tacky build-up on triangular prong of table mounted can opener. Observed minor amount of black mildew like build-up on back part of divider in crushed ice machine. Remove build-up; clean and sanitize.
ROACHY SAYS:
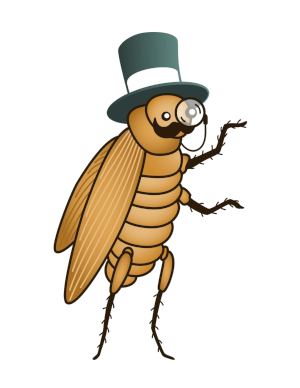
“Food-contact surfaces and utensils shall be clean to sight and touch. Food-contact surfaces and multiservice utensils shall be effectively washed, rinsed, and sanitized to remove or completely loosen soils by use of manual or mechanical methods. Precleaning may be required. Manual sanitization shall be accomplished during the final rinse by contact with solution containing 100 ppm available chlorine, 200 ppm quaternary ammonium, or another approved sanitizer. Mechanical sanitization shall be accomplished in the final rinse by achieving a utensil surface temperature of 160F or by contact with solution containing 50 ppm available chlorine, 200 ppm quaternary ammonium, or another approved sanitizer. After cleaning and sanitizing, equipment and utensils shall be air dried. Mechancial warewash machines must be approved and installed and operated according to manufacturer's specifications. Food contact surfaces, utensils, and equipment shall be cleaned and sanitized at the following times: before each use with different type of raw food of animal origin, when changing from raw food to ready to eat food, between uses with raw produce and potentially hazardous food, before using a thermometer, and any time during the operation when contamination may have occurred. Warewash sinks used to wash wiping cloths, wash produce, or thaw food must be cleaned and sanitized before and after these uses. Equipment, food contact surfaces, and utensils must be cleaned and sanitized throughout the day at least every four hours or as needed to prevent contamination. (114097, 114099.1, 114099.2, 114099.4, 114099.6, 114099.7, 114101, 114105, 114109, 114111, 114113, 114115(a,c), 114117, 114125(b), 114141)”
17. Compliance with shell stock tags, condition, display.
Conditions Observed: Observed one bin in walkin lacked shell stock tag. Keep tag with oysters. Observed stock tags to be disorganized. As discussed during the inspection, store stock tags in chronological order. Label tags with the dates those shell stock were sold.
ROACHY SAYS:
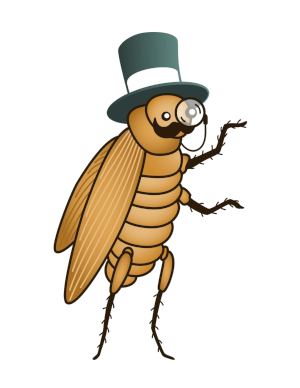
“Shellstock shall be obtained in containers that bear legible source identification tags. A food facility shall ensure that shellstock from one tagged or labeled container are not commingled with shellstock from another container with different certification numbers. Shellstock tags shall remain attached to the container that they are received in until the container is empty. The identity of the source of the shellstock sold or served shall be maintained for 90 days from the dates of harvest by using an approved recordkeeping system that keeps the tags or labels in chronological order correlated to the date or dates the shellstock is sold or served. The source of the shellstock on display shall be identified. Shellstock that are portioned or prepackaged shall have a copy of the corresponding shellstock tag. Except in accordance with an approved HACCP plan, molluscan shellfish life-support system display tanks shall not be used to display shellfish that are offered for human consumption. (114039-114039.5)”
22. Hot and Cold Water Available
Conditions Observed: Measured hot water at the bar to be 117.5 F. Adjust/service/repair to deliver hot water at 120 F or greater.
ROACHY SAYS:
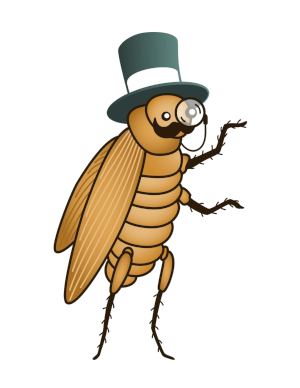
“An adequate, protected, pressurized, approved potable supply of hot and cold water shall be provided at all times. Hot water shall be supplied at a minimum temperature of 120F when measured from the faucet. The temperature of water provided to handwashing facilities shall be at least 100F. Handwashing facilities equipped with non-adjustable faucets shall have their temperature set between 100F and 108F. Hot water shall be provided at the food preparation sink and janitorial sink. (113953(c), 114099.2(b), 114163(a)(3), 114189, 114192, 114192.1, 114195)”
43. Toilet facilities: properly constructed, supplied, cleaned.
Conditions Observed: Bathroom door is not self-closing. Repair door to be self-closing.
ROACHY SAYS:
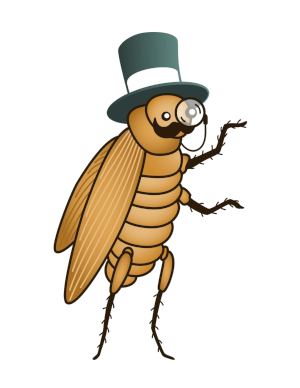
“Toilet facilities shall be maintained and kept clean. Toilet rooms shall be separated by a well-fitting, self-closing door. Toilet tissue shall be provided in a permanently installed dispenser at each toilet. (114250, 114250.1, 114276)”
Tuesday, July 16, 2019 (1 violation)
Reinspection
06. Hands clean and properly washed; gloves used properly.
Conditions Observed: Observed Dishwasher arrive for shift, check in with Kitchen Manager, and then proceed to 3part sink. Inspector intervened and instructed dishwasher to wash hands upon arriving for work, before washing dishes, always before putting up clean and sanitized dishes. Observed correct handwashing by dishwasher - COS. Reviewed handwashing worksheets - cookline staff have recieved training in complaint handwashing. Provided facility with CalCode section 113953.3 - please review with all kitchen staff. Discussed handwashing as food safety focus. This is violation is corrected.
ROACHY SAYS:
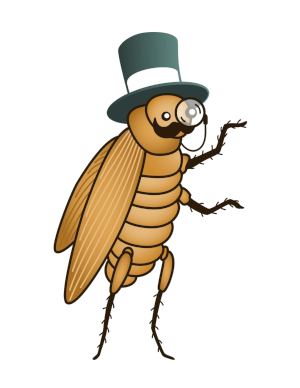
“Food employees shall minimize bare hand and arm contact with nonprepackaged food that is in ready to eat form. Whenever gloves are worn, they shall be changed, replaced, or washed as often as handwashing is required. Single-use gloves shall not be washed. Employees shall wash their hands in the following situations: immediately before engaging in food preparation including working with nonprepackaged food, clean equipment and utensils and unwrapped single-use food containers and utensils; after touching bare human body parts other than clean hands and clean exposed portions of arms; after using the toilet room; after caring for or handling any animal; after coughing, sneezing, using a handkerchief or disposable tissue, using tobacco, eating or drinking; after handling soiled equipment or utensils; during food preparation, as often as necessary to remove soil and contamination and to prevent cross-contamination when changing tasks; when switching from working with raw food and working with ready-to-eat foods; before initially donning gloves for working with food; before dispensing or serving food handling clean tableware and serving utensils in the food service area; after engaging in other activities that contaminate the hands. (113952, 113953.3, 113953.4, 113961, 113968, 113973)”
Wednesday, July 10, 2019 (7 violations)
Routine Inspection
06. Hands clean and properly washed; gloves used properly.
Conditions Observed: Observed Cook put raw oysters on the grill and then proceed with food handling. Always wash hands after handling raw oysters and raw animal proteins. Please retrain cookline staff in complaint handwashing. See handout provided. This violation requires a reinspection on/after 7/15/19.
ROACHY SAYS:
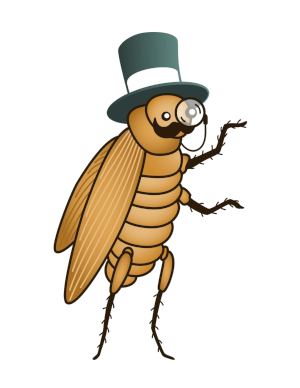
“Food employees shall minimize bare hand and arm contact with nonprepackaged food that is in ready to eat form. Whenever gloves are worn, they shall be changed, replaced, or washed as often as handwashing is required. Single-use gloves shall not be washed. Employees shall wash their hands in the following situations: immediately before engaging in food preparation including working with nonprepackaged food, clean equipment and utensils and unwrapped single-use food containers and utensils; after touching bare human body parts other than clean hands and clean exposed portions of arms; after using the toilet room; after caring for or handling any animal; after coughing, sneezing, using a handkerchief or disposable tissue, using tobacco, eating or drinking; after handling soiled equipment or utensils; during food preparation, as often as necessary to remove soil and contamination and to prevent cross-contamination when changing tasks; when switching from working with raw food and working with ready-to-eat foods; before initially donning gloves for working with food; before dispensing or serving food handling clean tableware and serving utensils in the food service area; after engaging in other activities that contaminate the hands. (113952, 113953.3, 113953.4, 113961, 113968, 113973)”
08. Proper hot and cold holding temperatures.
Conditions Observed: Measured foods held in ice baths to be 50 F; Kitchen Manager began discarding foods. Reviewed best practice for cold holding with ice baths. This violation requires a reinspection on/after 7/15/19. Measured foods in the deli preps to be above 41 F (past, 49 F, crushed garlic 49 F; sliced carrot, 45 F, cooked shrimp 45 F). Adjust/service/repair to cold-hold at or below 41 F. No temperature control for sliced fruit and veggie garnishes at the bar. Keep garnishes and juices at or below 41 F.
ROACHY SAYS:
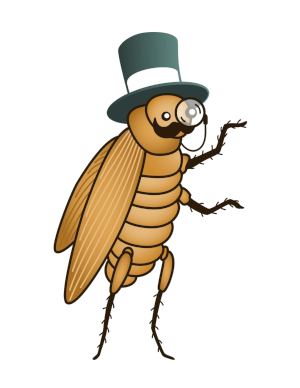
“Except during preparation, cooking, cooling, transportation to or from a retail food facility for a period of less than thirty minutes, when time is used as the public health control, or as otherwise specified, potentially hazardous foods shall be maintained at or below 41F or at or above 135F. The following foods may be held at or below 45F: raw shell eggs, unshucked live molluscan shellfish, pasteurized milk and pasteurized milk products in original sealed containers, potentially hazardous foods held during transportation. Potentially hazardous foods held for dispensing in serving lines and salad bars may be held at 45F, not to exceed 12 hours in a 24 hour period, if unused portions are discarded. Food preparation shall not exceed two cumulative hours without a return to the required holding temperatures. (113996, 113998, 114037, 114343(a))”
15. Food contact surfaces: clean and sanitized.
Conditions Observed: No chlorine in the dishwasher at the beginning of the inspection. Kitchen Manager adjusted tubing and primed the line; measured chlorine to be 50 PPM. COS. Train all dishwashers to use test strips daily and to report deficiencies to the Kitchen Manager. Observed black, mildew-like build-up on the side of the ice machine. Remove build-up; clean and sanitize. This violation requires a reinspection on/after 7/15/19.
ROACHY SAYS:
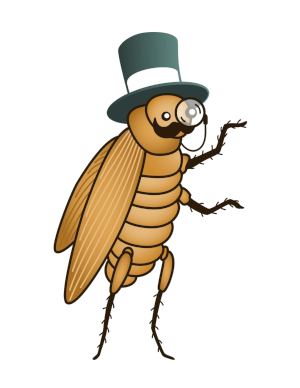
“Food-contact surfaces and utensils shall be clean to sight and touch. Food-contact surfaces and multiservice utensils shall be effectively washed, rinsed, and sanitized to remove or completely loosen soils by use of manual or mechanical methods. Precleaning may be required. Manual sanitization shall be accomplished during the final rinse by contact with solution containing 100 ppm available chlorine, 200 ppm quaternary ammonium, or another approved sanitizer. Mechanical sanitization shall be accomplished in the final rinse by achieving a utensil surface temperature of 160F or by contact with solution containing 50 ppm available chlorine, 200 ppm quaternary ammonium, or another approved sanitizer. After cleaning and sanitizing, equipment and utensils shall be air dried. Mechancial warewash machines must be approved and installed and operated according to manufacturer's specifications. Food contact surfaces, utensils, and equipment shall be cleaned and sanitized at the following times: before each use with different type of raw food of animal origin, when changing from raw food to ready to eat food, between uses with raw produce and potentially hazardous food, before using a thermometer, and any time during the operation when contamination may have occurred. Warewash sinks used to wash wiping cloths, wash produce, or thaw food must be cleaned and sanitized before and after these uses. Equipment, food contact surfaces, and utensils must be cleaned and sanitized throughout the day at least every four hours or as needed to prevent contamination. (114097, 114099.1, 114099.2, 114099.4, 114099.6, 114099.7, 114101, 114105, 114109, 114111, 114113, 114115(a,c), 114117, 114125(b), 114141)”
22. Hot and Cold Water Available
Conditions Observed: Measured water at the 3part sink to be 117 F. Adjust/service/repair to deliver hot water at 120 F or greater.
ROACHY SAYS:
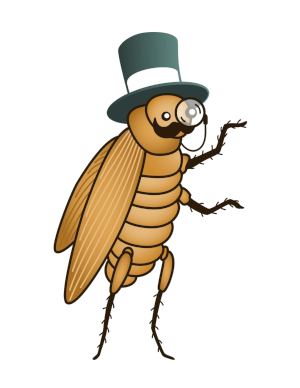
“An adequate, protected, pressurized, approved potable supply of hot and cold water shall be provided at all times. Hot water shall be supplied at a minimum temperature of 120F when measured from the faucet. The temperature of water provided to handwashing facilities shall be at least 100F. Handwashing facilities equipped with non-adjustable faucets shall have their temperature set between 100F and 108F. Hot water shall be provided at the food preparation sink and janitorial sink. (113953(c), 114099.2(b), 114163(a)(3), 114189, 114192, 114192.1, 114195)”
31. Food storage; food storage containers identified.
Conditions Observed: Observed bags of flour, rice on the ground in the dry storage area. Store all food at least 6 inches off the ground. Consider keeping all opened bulk foods in a lidded, NSF-approved food storage container.
ROACHY SAYS:
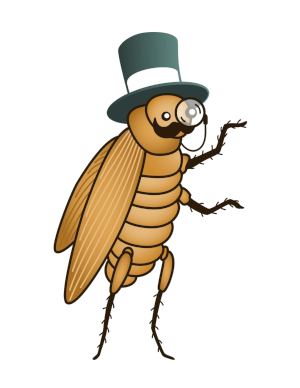
“Adequate and suitable space shall be provided for the storage of food. Food shall be protected from contamination by storing the food in a clean, dry location, where it is not exposed to splash, dust, vermin, or other forms of contamination or adulteration, and at least six inches above the floor. Food shall not be stored in any of the following ways: in locker rooms, toilet rooms, dressing rooms, refuse rooms, mechanical rooms, under sewer lines that are not shielded to intercept potential drips, under leaking water lines, including leaking automatic fire sprinklers heads, or under lines on which water has condensated, under open stairwells or under sources of contamination. Working containers holding food or food ingredients that are removed from their original packages for use in the food facility shall be identified with the common name of the food. Non-prepackaged food may not be stored in direct contact with undrained ice. Products that are held by the permit holder for credit, redemption, or return to the distributor, such as damaged, spoiled, or recalled products shall be segregated and held in designated areas that are separated from food, equipment, utensils, linens, and single-use articles. (114047, 141049, 114051, 114053, 114055, 114067(h), 114069(b))”
43. Toilet facilities: properly constructed, supplied, cleaned.
Conditions Observed: Observed door to restroom was open upon arrival. Repair door to be self-closing.
ROACHY SAYS:
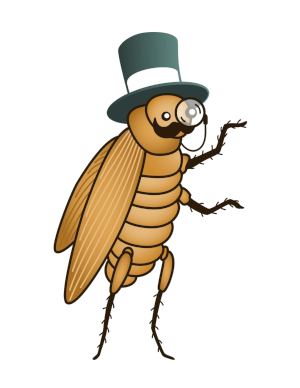
“Toilet facilities shall be maintained and kept clean. Toilet rooms shall be separated by a well-fitting, self-closing door. Toilet tissue shall be provided in a permanently installed dispenser at each toilet. (114250, 114250.1, 114276)”
44. Premises; personal/cleaning items; vermin-proofing.
Conditions Observed: Observed backpacks and similar personal items stored on shelf in dry storage area. Provide a designated area for personal belongings.
ROACHY SAYS:
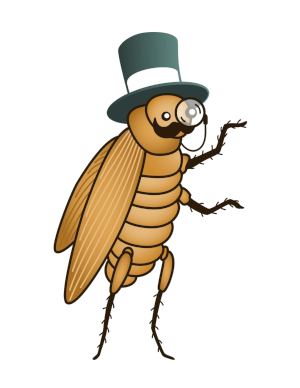
“All premises of a food facility shall be kept clean, fully operative, and in good repair. The premise of a food facility shall be free of litter and items unnecessary to the operation of the facility. Areas designated for employees to eat and drink shall be located so that food, clean equipent and utensils, linens, and single-use articles are protected from contamination. Personal items shall be stored in a designated area to prevent contamination of food or utensils. Food prep sinks, warewashing sinks, and handwashing sinks shall not be used for the cleaning or maintenance of tools or cleaning supplies or to dispose of mop water and similar liquid wastes. A dedicated janitorial sink with a drain shall be provided and conveniently located. A separate room, area, or cabinet shall be provided for cleaning supplies. The facility shall be kept vermin proof. Insect electrocution devices shall retain the insect within the device and shall not be located over food or utensil handling areas. (114123, 114143(a, b), 114256, 114256.1, 114256.2, 114256.4, 114257, 114257.1, 114259, 114259.2, 114259.3, 114279, 114281, 114282)”
Thursday, Feb. 7, 2019 (5 violations)
Routine Inspection
06. Hands clean and properly washed; gloves used properly.
Conditions Observed: Observed Cook add cabbage to fish tacos with their bare hand. Use a clean utensil to add ready-to-eat foods like veggies to plates.
ROACHY SAYS:
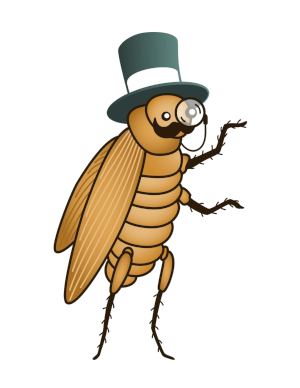
“Food employees shall minimize bare hand and arm contact with nonprepackaged food that is in ready to eat form. Whenever gloves are worn, they shall be changed, replaced, or washed as often as handwashing is required. Single-use gloves shall not be washed. Employees shall wash their hands in the following situations: immediately before engaging in food preparation including working with nonprepackaged food, clean equipment and utensils and unwrapped single-use food containers and utensils; after touching bare human body parts other than clean hands and clean exposed portions of arms; after using the toilet room; after caring for or handling any animal; after coughing, sneezing, using a handkerchief or disposable tissue, using tobacco, eating or drinking; after handling soiled equipment or utensils; during food preparation, as often as necessary to remove soil and contamination and to prevent cross-contamination when changing tasks; when switching from working with raw food and working with ready-to-eat foods; before initially donning gloves for working with food; before dispensing or serving food handling clean tableware and serving utensils in the food service area; after engaging in other activities that contaminate the hands. (113952, 113953.3, 113953.4, 113961, 113968, 113973)”
08. Proper hot and cold holding temperatures.
Conditions Observed: Measured foods to be above 41 in the top right deli prep (kale, 49 F; sauce, 43.5 F). Observed inserts containing food resting in large stainless steel tray. Measure food in the top left deli prep to be above 41 F (salsa, 45 F; potato, 45 F). Revise cold-holding method to keep food in direct contact with refrigeration and at or below 41 F.
ROACHY SAYS:
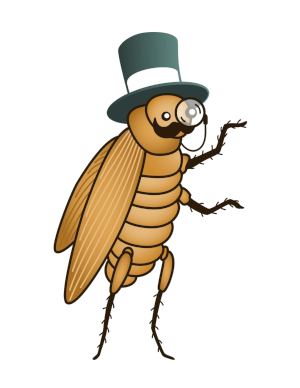
“Except during preparation, cooking, cooling, transportation to or from a retail food facility for a period of less than thirty minutes, when time is used as the public health control, or as otherwise specified, potentially hazardous foods shall be maintained at or below 41F or at or above 135F. The following foods may be held at or below 45F: raw shell eggs, unshucked live molluscan shellfish, pasteurized milk and pasteurized milk products in original sealed containers, potentially hazardous foods held during transportation. Potentially hazardous foods held for dispensing in serving lines and salad bars may be held at 45F, not to exceed 12 hours in a 24 hour period, if unused portions are discarded. Food preparation shall not exceed two cumulative hours without a return to the required holding temperatures. (113996, 113998, 114037, 114343(a))”
10. Proper cooling methods.
Conditions Observed: Measured pasta dated 2/5 to 48 F. Operator discarded pasta - COS. Reviewed rapid cooling with Kitchen Manager. Revise cooling method to ensure that all advance prep foods are at or below 41 F before transferring to cambros.
ROACHY SAYS:
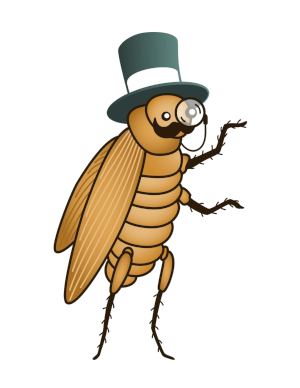
“After heating, potentially hazardous foods shall be rapidly cooled from 135F to 70F within 2 hours, and then from 70F to 41F within 4 hours. Potentially hazardous foods prepared from ambient temperature ingredients must be cooled to below 41F within 4 hours. Cooling shall be facilitated by one or more of the following methods: in shallow pans, separating food into smaller portions, adding ice as an ingredient, using an ice bath and stirring frequently, using an ice paddle, using rapid cooling equipment, or using containers that facilitate heat transfer. (114002, 114002.1)”
15. Food contact surfaces: clean and sanitized.
Conditions Observed: Measured 0 PPm chlorine in dishwasher today. Observed bulk sanitizer bin to be empty - showed observations to Kitchen Manager. Train dishwasher to use chlorine test strips daily. Dishwasher replaced sanitizer and primed machine. Measured chlorine to be 50 PPM. COS. Observed bar tender dunk and them immediate remove glasses from QT solution at sanitizing bin. Soak glasses and all utensils for at at least 60 seconds as per manufacturer’s instructions. Bartender returned glasses to sanitizing solution. COS. Observed build-up/food debris on the following food contact surfaces: the white divider in the crushed ice machine, on the prong of the table mounted can opener, and on the potato cutter. Remove build-up; clean and sanitize. Clean routinely to avoid build-up.
ROACHY SAYS:
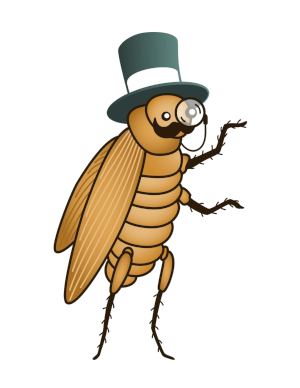
“Food-contact surfaces and utensils shall be clean to sight and touch. Food-contact surfaces and multiservice utensils shall be effectively washed, rinsed, and sanitized to remove or completely loosen soils by use of manual or mechanical methods. Precleaning may be required. Manual sanitization shall be accomplished during the final rinse by contact with solution containing 100 ppm available chlorine, 200 ppm quaternary ammonium, or another approved sanitizer. Mechanical sanitization shall be accomplished in the final rinse by achieving a utensil surface temperature of 160F or by contact with solution containing 50 ppm available chlorine, 200 ppm quaternary ammonium, or another approved sanitizer. After cleaning and sanitizing, equipment and utensils shall be air dried. Mechancial warewash machines must be approved and installed and operated according to manufacturer's specifications. Food contact surfaces, utensils, and equipment shall be cleaned and sanitized at the following times: before each use with different type of raw food of animal origin, when changing from raw food to ready to eat food, between uses with raw produce and potentially hazardous food, before using a thermometer, and any time during the operation when contamination may have occurred. Warewash sinks used to wash wiping cloths, wash produce, or thaw food must be cleaned and sanitized before and after these uses. Equipment, food contact surfaces, and utensils must be cleaned and sanitized throughout the day at least every four hours or as needed to prevent contamination. (114097, 114099.1, 114099.2, 114099.4, 114099.6, 114099.7, 114101, 114105, 114109, 114111, 114113, 114115(a,c), 114117, 114125(b), 114141)”
39. Thermometers provided and accurate.
Conditions Observed: Unable to locate a thermometer in the single door fridge at the cookline. Provide a thermometer for this unit.
ROACHY SAYS:
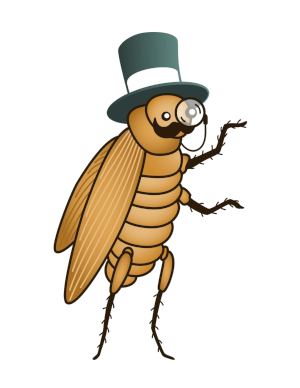
“An accurate easily readable metal probe thermometer suitable for measuring temperature of food shall be available to the food handler. Thermometers shall be calibrated in accordance with manufacturer's specifications as necessary to ensure their accuracy. A thermometer +/- 2 degrees F shall be provided for all refrigerators, hot and cold holding units, and high temperature warewashing machines. (114157, 114159)”