Ecos Cafe
Sequoia Park Zoo Foundation
3414 W St, Eureka
Thursday, Sept. 2, 2021 (3 violations)
Routine Inspection
02. Food safety certification, food handler card compliance
Conditions Observed: Food Safety Manager (FSM) on file with this office is no longer employed at the facility. Obtain FSM certification within 60 days and make available during routine food inspections. Food handler cards for all other employees are not kept on record at the facility. Obtain food handler cards within 30 days and make available during routine food inspections.
ROACHY SAYS:
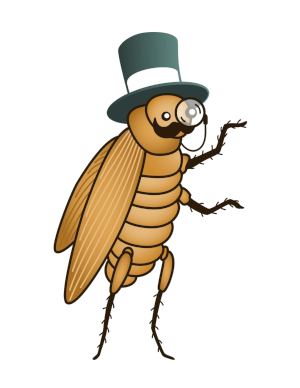
“Food facilities that prepare, handle, or serve non-prepackaged potentially hazardous food, shall have an owner or employee who has passed an aproved food safety certification examination. Food handlers that prepare, handle, or serve non-prepackaged potentially hazardous food, shall obtain a valid Food Handler Card within 30 days after date of hire. (113947.1-113947.5, 113948)”
06. Hands clean and properly washed; gloves used properly.
Conditions Observed: Observed gloved employee handle raw chicken, remove glove, then handle sanitized utensils without handwashing. Handwashing is required after handling raw meat and prior to handling sanitized utensils. Instructed employee to handwash, this major violation was corrected.
ROACHY SAYS:
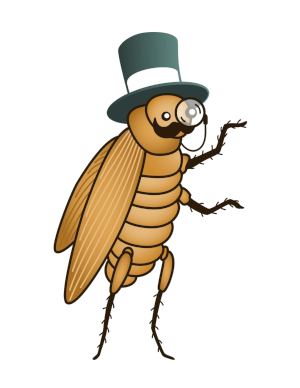
“Food employees shall minimize bare hand and arm contact with nonprepackaged food that is in ready to eat form. Whenever gloves are worn, they shall be changed, replaced, or washed as often as handwashing is required. Single-use gloves shall not be washed. Employees shall wash their hands in the following situations: immediately before engaging in food preparation including working with nonprepackaged food, clean equipment and utensils and unwrapped single-use food containers and utensils; after touching bare human body parts other than clean hands and clean exposed portions of arms; after using the toilet room; after caring for or handling any animal; after coughing, sneezing, using a handkerchief or disposable tissue, using tobacco, eating or drinking; after handling soiled equipment or utensils; during food preparation, as often as necessary to remove soil and contamination and to prevent cross-contamination when changing tasks; when switching from working with raw food and working with ready-to-eat foods; before initially donning gloves for working with food; before dispensing or serving food handling clean tableware and serving utensils in the food service area; after engaging in other activities that contaminate the hands. (113952, 113953.3, 113953.4, 113961, 113968, 113973)”
12. Proper reheating procedures for hot holding.
Conditions Observed: Measured cheese sauce 51F reheating in Carnival King food warmer. Potentially hazardous foods must be reheated to at least 165F for at least 15 seconds prior to being put into a hot holding unit. Instructed employees to reheat cheese sauce on stove or in the microwave to at least 165F. This major violation was corrected.
ROACHY SAYS:
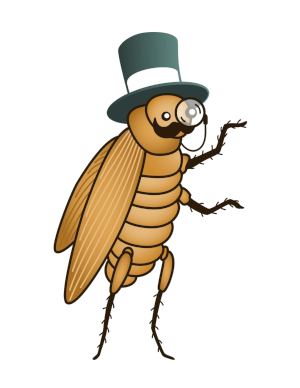
“Potentinally hazardous food that is cooked, cooled, and reheated for hot holding shall be heated to a temperature of 165F for 15 seconds. Cooked and refrigerated food that is prepared for immediate service in response to an individual consumer order may be served at any temperature. Reheating for hot holding shall be done rapidly, and the time between 41F and 165F shall not exceed two hours. Potentinally hazardous food reheated in a microwave oven for hot holding shall be rotated or stirred midway during cooking, covered to retain surface moisture, be reheated to 165F in all parts of the food, and stand covered for at least two minutes after reheating. Ready-to-eat food taken from a commercailly processed hermetically sealed container or from an intact package from a food processing plant shall be heated to a temperature of 135F for hot holding. (114014, 114016)”
Thursday, March 18, 2021 (0 violations)
Routine Inspection
ROACHY SAYS:
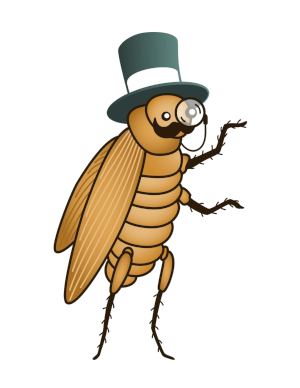
“Take a victory lap, Ecos Cafe! In the race that is maintaining a clean and healthy establishment you've earned Roachy's gold medal! Eat here today, everyone!!”
Friday, Sept. 25, 2020 (0 violations)
Routine Inspection
ROACHY SAYS:
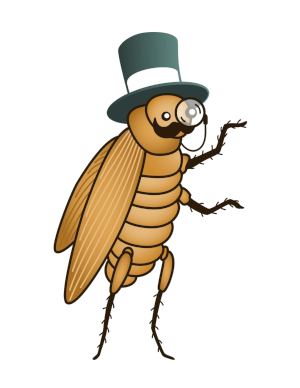
“Wow! Roachy can see himself in your butterknives! Way to go, Ecos Cafe!!”
Friday, Aug. 7, 2020 (0 violations)
CP - Change of Ownership
ROACHY SAYS:
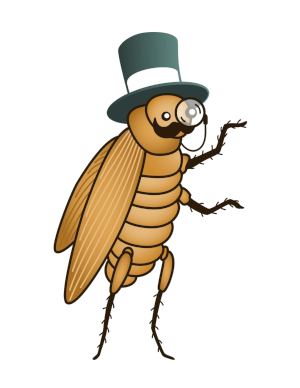
“Ooo! Welcome to Sanitarytown! Population: Ecos Cafe! I see lots of happy hungry mouths in this establishment's near future!!”
Tuesday, Jan. 28, 2020 (2 violations)
Routine Inspection
08. Proper hot and cold holding temperatures.
Conditions Observed: Measured ground beef 109.5F with probe thermometer in hot hold unit. Per operator, the hot hold unit was turned down, by mistake. It was unknown how long the temperature had been turned down on the hot hold unit. Monitor temperatures frequently to verify hot foods are held at or above 135F and cold foods are held at or below 41F. Operator discarded approximately 1 cup of ground beef, this major violation was corrected, thank you. Measured whole milk 46.5F with probe thermometer in carafe held out of temperature control. You may hold the whole milk out of temperature control if it is time labeled for 4 hours then discarded after 4 hours has past, or hold whole milk under temperature control, in a refrigerator or an ice bath, at or below 41F at all times. Operator will use a digital timer to hold the milk out of temperature control for 4 hours then will discard after 4 hours has past, this minor violation was corrected. Measured Polish dog 43.5F and hot dog 42.5F with probe thermometer in prep table middle, and bottom drawers. Adjust/service/repair prep table, bottom portion, to hold cold potentially hazardous foods at or below 41F at all times.
ROACHY SAYS:
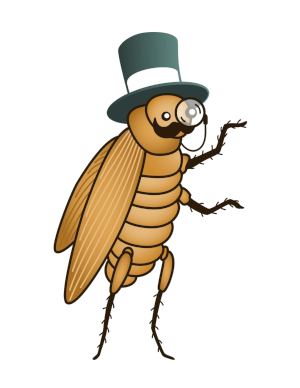
“Except during preparation, cooking, cooling, transportation to or from a retail food facility for a period of less than thirty minutes, when time is used as the public health control, or as otherwise specified, potentially hazardous foods shall be maintained at or below 41F or at or above 135F. The following foods may be held at or below 45F: raw shell eggs, unshucked live molluscan shellfish, pasteurized milk and pasteurized milk products in original sealed containers, potentially hazardous foods held during transportation. Potentially hazardous foods held for dispensing in serving lines and salad bars may be held at 45F, not to exceed 12 hours in a 24 hour period, if unused portions are discarded. Food preparation shall not exceed two cumulative hours without a return to the required holding temperatures. (113996, 113998, 114037, 114343(a))”
15. Food contact surfaces: clean and sanitized.
Conditions Observed: Measured chlorine sanitizer 0PPM in cookline sanitizer bucket. Use test strips to verify the chlorine sanitizer is at the correct concentration of 100PPM each time sanitizer is made and change when it becomes visibly soiled or falls below the required concentration to effectively sanitize food-contact surfaces. Operator replenished chlorine sanitizer solution that measured 100PPM, this major violation was corrected.
ROACHY SAYS:
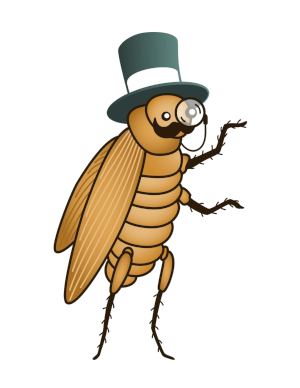
“Food-contact surfaces and utensils shall be clean to sight and touch. Food-contact surfaces and multiservice utensils shall be effectively washed, rinsed, and sanitized to remove or completely loosen soils by use of manual or mechanical methods. Precleaning may be required. Manual sanitization shall be accomplished during the final rinse by contact with solution containing 100 ppm available chlorine, 200 ppm quaternary ammonium, or another approved sanitizer. Mechanical sanitization shall be accomplished in the final rinse by achieving a utensil surface temperature of 160F or by contact with solution containing 50 ppm available chlorine, 200 ppm quaternary ammonium, or another approved sanitizer. After cleaning and sanitizing, equipment and utensils shall be air dried. Mechancial warewash machines must be approved and installed and operated according to manufacturer's specifications. Food contact surfaces, utensils, and equipment shall be cleaned and sanitized at the following times: before each use with different type of raw food of animal origin, when changing from raw food to ready to eat food, between uses with raw produce and potentially hazardous food, before using a thermometer, and any time during the operation when contamination may have occurred. Warewash sinks used to wash wiping cloths, wash produce, or thaw food must be cleaned and sanitized before and after these uses. Equipment, food contact surfaces, and utensils must be cleaned and sanitized throughout the day at least every four hours or as needed to prevent contamination. (114097, 114099.1, 114099.2, 114099.4, 114099.6, 114099.7, 114101, 114105, 114109, 114111, 114113, 114115(a,c), 114117, 114125(b), 114141)”
Friday, Sept. 20, 2019 (2 violations)
Routine Inspection
28. Food separated and protected.
Conditions Observed: Observed raw shell eggs stored over ready-to-eat foods in Traulsen 2 door refrigerator. Store raw potentially hazardous foods under ready-to-eat foods based on final internal cooking temperatures to prevent cross-contamination. The eggs were moved to the bottom shelf, thank you.
ROACHY SAYS:
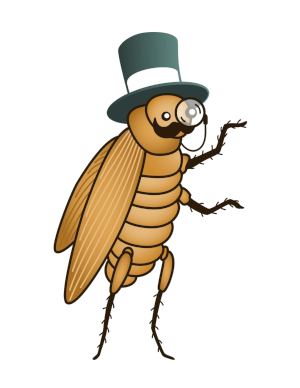
“Food shall be protected from contamination during transportation, storage, preparation, holding, and display. Adequate and suitable counter space shall be provided for all food preparation. Food preparation shall be conducted wthin an approved food compartment or fully enclosed food facility. Open-air barbecues shall be separated from public access. (113984(a-f), 113986, 114060, 114067(a,d,e,j), 114069(a, c, d), 114077, 114089.1(c), 114143(c,e))”
36. Equipment / Utensils approved; installed, clean, good repair, capacity.
Conditions Observed: Observed single-use plastic cup used to portion bulk sugar. Obtain approved utensils, with handles, and store with handles facing up out of contact with food to prevent cross-contamination. The single-use utensil was discarded, thank you.
ROACHY SAYS:
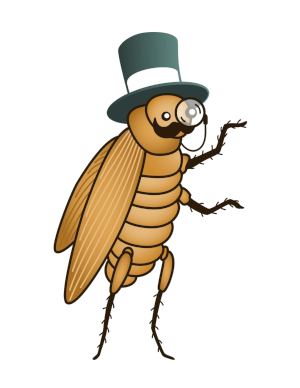
“Utensils and equipment shall be kept fully operative and in good repair. All new and replacement equipment shall be properly installed and be certified or classified for sanitation by an ANSI accredited certification program. Electrical appliances must meet UL standards. Single-use articles shall not allow migration of deleterious substances or impart colors, odors, or tastes to food. Multi-use food contact surfaces must be smooth, free of breaks, chips, and similar imperfections; free of sharp internal angles, corners, and crevices; finished to have smooth welds and joints; be accessible for cleaning and inspection. Unless specified, wood and wood wicker may not be used as a food-contact surface. Unless specified, copper and copper alloys such as brass may not be used in contact with a food that has a pH below six or for a fitting between a backflow preventer and a carbonator. Beverage tubing and cold-plate beverage cooling devices cannot be installed in contact with stored ice intended to be used as food. Equipment that is not movable must be installed to allow for cleaning in place. Cutting or piercing parts of can openers must be readily removable. Facilities that wash, rinse, soak, thaw, or similarly prepare foods shall be provided with a approved food preparation sink. Reservoirs that supply water to produce foggers must be cleaned and maintained. Surfaces such as cutting blocks and boards that are subject to scratching and scoring shall be resurfaced or replaced if they can no longer be effectively cleaned and sanitized. (114130, 114130.1, 114130.2, 114130.3, 114130.4, 114130.5, 114130.6, 114132, 114133, 114137, 114139, 114153, 114163, 114165, 114167, 114169, 114175, 114177, 114180, 114182)”
Monday, March 25, 2019 (1 violation)
Routine Inspection
37. Equipment, utensils and linens: storage and use.
Conditions Observed: Observed ice cream scoop stored in standing water held at room temperature. The ice cream utensil shall be held in running water of sufficient velocity to flush particulates to a drain. Consider obtaining a dipper well for correct storage of ice cream utensil.
ROACHY SAYS:
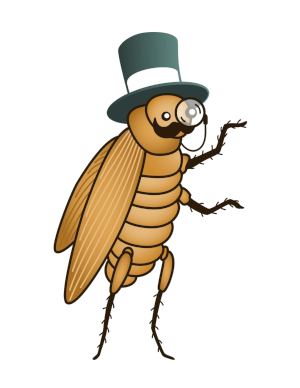
“Clean equipment, utensils, linens, and single-use articles shall be stored at least six inches above the floor in an approved location within the fully enclosed permitted food facility. Clean equipment, utensils, linens, and single-use articles shall not be exposed to splash, dust, vermin, or other forms of contamination. Non-food items shall be stored and displayed separate from food and food-contact surfaces. During pauses in food preparation utensils shall be stored with handles above the top of the food, on a clean sanitized surface, in running water, or in water that is at least 135øF. Single-use articles and multiservice utensils shall be handled, displayed, and dispensed so that contamination of food and lip-contact surfaces is prevented. Extra preset tableware shall be removed when a consumer is seated or cleaned and sanitized before further use. Pressurized cylinders shall be securely fastened to rigid structure. Linens must be free of food residue and soil and be laundered as required. (114074, 114075(a,b,d,e), 114081, 114119, 114121, 114161, 114172, 114178, 114179, 114083, 114185, 114185.2, 114185.3, 114185.4, 114185.5)”
Friday, Nov. 16, 2018 (1 violation)
Routine Inspection
36. Equipment / Utensils approved; installed, clean, good repair, capacity.
Conditions Observed: Observed mold like substance in the ice machine. Clean and sanitize ice machine per manufacturer’s instructions to prevent mold growth.
ROACHY SAYS:
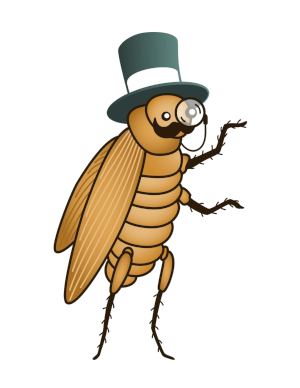
“Utensils and equipment shall be kept fully operative and in good repair. All new and replacement equipment shall be properly installed and be certified or classified for sanitation by an ANSI accredited certification program. Electrical appliances must meet UL standards. Single-use articles shall not allow migration of deleterious substances or impart colors, odors, or tastes to food. Multi-use food contact surfaces must be smooth, free of breaks, chips, and similar imperfections; free of sharp internal angles, corners, and crevices; finished to have smooth welds and joints; be accessible for cleaning and inspection. Unless specified, wood and wood wicker may not be used as a food-contact surface. Unless specified, copper and copper alloys such as brass may not be used in contact with a food that has a pH below six or for a fitting between a backflow preventer and a carbonator. Beverage tubing and cold-plate beverage cooling devices cannot be installed in contact with stored ice intended to be used as food. Equipment that is not movable must be installed to allow for cleaning in place. Cutting or piercing parts of can openers must be readily removable. Facilities that wash, rinse, soak, thaw, or similarly prepare foods shall be provided with a approved food preparation sink. Reservoirs that supply water to produce foggers must be cleaned and maintained. Surfaces such as cutting blocks and boards that are subject to scratching and scoring shall be resurfaced or replaced if they can no longer be effectively cleaned and sanitized. (114130, 114130.1, 114130.2, 114130.3, 114130.4, 114130.5, 114130.6, 114132, 114133, 114137, 114139, 114153, 114163, 114165, 114167, 114169, 114175, 114177, 114180, 114182)”