Southside Mike's BBQ
Trailer
100 Ericson CT, Arcata
Friday, Oct. 29, 2021 (4 violations)
Routine Inspection
06. Hands clean and properly washed; gloves used properly.
Conditions Observed: Observed operator don gloves without handwashing. Handwashing is required prior to donning gloves. Operator removed gloves and conducted a handwash; handwashing was demonstrated over the duration of the inspection.
ROACHY SAYS:
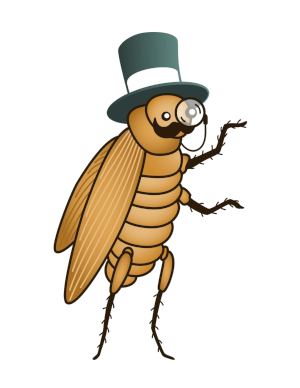
“Food employees shall minimize bare hand and arm contact with nonprepackaged food that is in ready to eat form. Whenever gloves are worn, they shall be changed, replaced, or washed as often as handwashing is required. Single-use gloves shall not be washed. Employees shall wash their hands in the following situations: immediately before engaging in food preparation including working with nonprepackaged food, clean equipment and utensils and unwrapped single-use food containers and utensils; after touching bare human body parts other than clean hands and clean exposed portions of arms; after using the toilet room; after caring for or handling any animal; after coughing, sneezing, using a handkerchief or disposable tissue, using tobacco, eating or drinking; after handling soiled equipment or utensils; during food preparation, as often as necessary to remove soil and contamination and to prevent cross-contamination when changing tasks; when switching from working with raw food and working with ready-to-eat foods; before initially donning gloves for working with food; before dispensing or serving food handling clean tableware and serving utensils in the food service area; after engaging in other activities that contaminate the hands. (113952, 113953.3, 113953.4, 113961, 113968, 113973)”
07. Adequate handwash facilities supplied and accessible.
Conditions Observed: Observed handwash sink obstructed with take out containers. Maintain handwash sink unobstructed at all times for handwashing. Operator moved take out containers to another location.
ROACHY SAYS:
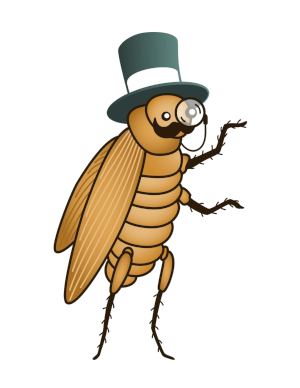
“Handwashing facilities shall be provided within or adjacent to toilet rooms, food preparation, and warewashing areas. Handwashing facilities shall be clean, unobstructed, and accessible at all times. Handwashing facilities shall be provided with soap and sanitary single use towels in approved dispensers. Dispensers shall be maintained in good repair. A handwashing facility shall not be used for purposes other than handwashing. (113953, 113953.1, 113953.2, 114067(f))”
08. Proper hot and cold holding temperatures.
Conditions Observed: Measured apple slaw 47F, and “special” dressing 46F in top portion of prep table. Measured marinated chicken 48F in bottom portion of prep table. Adjust/service/repair prep table to hold cold PHF at/below 41F at all times.
ROACHY SAYS:
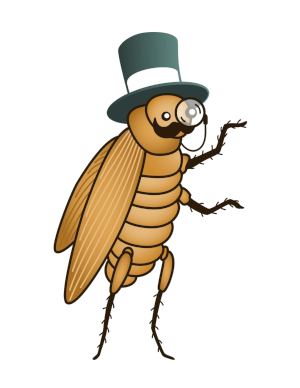
“Except during preparation, cooking, cooling, transportation to or from a retail food facility for a period of less than thirty minutes, when time is used as the public health control, or as otherwise specified, potentially hazardous foods shall be maintained at or below 41F or at or above 135F. The following foods may be held at or below 45F: raw shell eggs, unshucked live molluscan shellfish, pasteurized milk and pasteurized milk products in original sealed containers, potentially hazardous foods held during transportation. Potentially hazardous foods held for dispensing in serving lines and salad bars may be held at 45F, not to exceed 12 hours in a 24 hour period, if unused portions are discarded. Food preparation shall not exceed two cumulative hours without a return to the required holding temperatures. (113996, 113998, 114037, 114343(a))”
19. Compliance with variance, specialized process, reduced O2 packaging, HACCP plan.
Conditions Observed: Observed vacuum sealed meats in 2 door refrigerator. Vacuum sealing requires an approved HACCP plan from CDPH or you may be granted an exemption if the vacuum sealed PHF always complies with the following standards: 1. Food is labeled with production time and date 2. Food is held at/below 41F during refrigerated storage 3. Food is removed from its package in the food facility within 48 hours after packaging. Per operator, meats were vacuum sealed yesterday and will be used within 48 hours.
ROACHY SAYS:
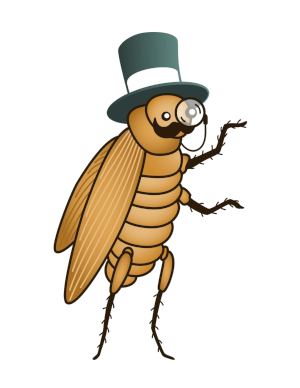
“A food facility may engage in the following activities only pursuant to a written and approved HACCP plan: smoking food as a method of preservation, curing food, using food additives or adding components such as vinegar as a method of food preservation or to render a food so that it is not potentially hazardous, operating a molluscan shelfish life support system display tank, custom processing of animals for personal use as food and not for sale or service in a food facility, using acidification or water activity to prevent the growth of Clostridium botulinum, packaging potentially hazardous food using a reduced oxygen packaging method except as specified in 114419.2(a - c), or preparing food by another method that is determined by the Enforcement Agency to require a HACCP plan. Food facilities with CDPH approved variances must maintain a copy at the food facility at all times. A variance may be suspended or revoked if the food facility is found to be non-complaint with the terms of the variance. (114057, 114057.1, 114417,114117.2, 114417.5, 114417.6, 114417.7, 114419 -114419.3)”
Thursday, April 11, 2019 (4 violations)
Routine Inspection
01. Demonstration of knowledge; food safety certification.
Conditions Observed: Food Safety Manager Certificate is not on file with DEH. Submit copy of certificate to this office via email or fax prior to 6/10/19 to avoid a reinspection.
ROACHY SAYS:
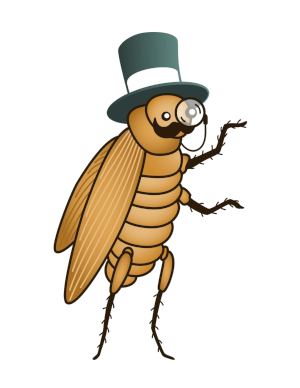
“The Person In Charge (PIC) and all employees shall have adequate knowledge and shall be properly trained in food safety as it relates to their assigned duties. The PIC shall have adequate knowledge of major food allergens, foods identified as major food allergens, and the symptoms that a major food allergen could cause. The PIC means a designated person who has knowledge of safe food handling practices and the major food allergens as they relate to the specific food preparation activities that occur at the food facility. (113947)”
15. Food contact surfaces: clean and sanitized.
Conditions Observed: Observed food debris on meat slicer. The meat slicer is a food contact surface that shall be washed and sanitized at least every 4 hours and after each use with raw potentially hazardous foods of animal origin to prevent cross-contamination.
ROACHY SAYS:
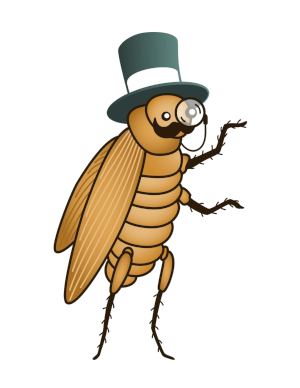
“Food-contact surfaces and utensils shall be clean to sight and touch. Food-contact surfaces and multiservice utensils shall be effectively washed, rinsed, and sanitized to remove or completely loosen soils by use of manual or mechanical methods. Precleaning may be required. Manual sanitization shall be accomplished during the final rinse by contact with solution containing 100 ppm available chlorine, 200 ppm quaternary ammonium, or another approved sanitizer. Mechanical sanitization shall be accomplished in the final rinse by achieving a utensil surface temperature of 160F or by contact with solution containing 50 ppm available chlorine, 200 ppm quaternary ammonium, or another approved sanitizer. After cleaning and sanitizing, equipment and utensils shall be air dried. Mechancial warewash machines must be approved and installed and operated according to manufacturer's specifications. Food contact surfaces, utensils, and equipment shall be cleaned and sanitized at the following times: before each use with different type of raw food of animal origin, when changing from raw food to ready to eat food, between uses with raw produce and potentially hazardous food, before using a thermometer, and any time during the operation when contamination may have occurred. Warewash sinks used to wash wiping cloths, wash produce, or thaw food must be cleaned and sanitized before and after these uses. Equipment, food contact surfaces, and utensils must be cleaned and sanitized throughout the day at least every four hours or as needed to prevent contamination. (114097, 114099.1, 114099.2, 114099.4, 114099.6, 114099.7, 114101, 114105, 114109, 114111, 114113, 114115(a,c), 114117, 114125(b), 114141)”
39. Thermometers provided and accurate.
Conditions Observed: Observed prep table lacking a thermometer. Install a readily visible thermometer in the warmest part of the refrigeration unit.
ROACHY SAYS:
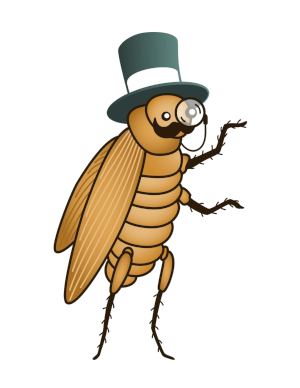
“An accurate easily readable metal probe thermometer suitable for measuring temperature of food shall be available to the food handler. Thermometers shall be calibrated in accordance with manufacturer's specifications as necessary to ensure their accuracy. A thermometer +/- 2 degrees F shall be provided for all refrigerators, hot and cold holding units, and high temperature warewashing machines. (114157, 114159)”
79. Mobile water and waste water tanks installed.
Conditions Observed: Observed grey hose for use to fill potable water tanks. Observed buildup and debris on threads of hose opening. Confirm the hose is food grade and remove bulidup/sanitize threads, or provide a hose that is clearly marked as food grade.
ROACHY SAYS:
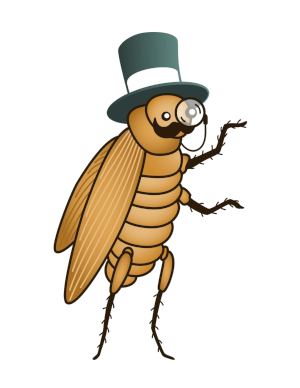
“MFFs that handle nonprepackaged food shall be equipped with approved potable water and wastewater tanks, unless approved temporary water and wastewater connections are provided. An approved potable water hose used for conveying potable water from a water tank shall be safe, durable, corrosion resistant, nonabsorbent, protected from contamination at all times, and clearly and durably identified as to its use. A potable water tank shall have sufficient capacity (at least 5 gallons exclusively for handwashing, 25 gallons for food preparation and warewashing) and shall deliver at least 1 gallon/minute to each sink basin. A wastewater tank shall be of a capacity commensurate with the level of food handling activity, have a minimum capacity that is 50 percent greater than the potable water tank, and be equipped with a shut-off valve. Wastewater tanks shall be thoroughly flushed and drained in a sanitary manner during the servicing operation. (114205, 114207, 114209, 114211, 114213, 114215, 114217, 114219, 114221, 114223, 114225, 114227, 114229, 114231, 114233, 114235, 114238, 114239, 114240, 114241, 114242)”