The Chalet House of Omelettes
1935 5th St, Eureka
Thursday, Nov. 14, 2019 (9 violations)
Routine Inspection
01. Demonstration of knowledge.
Conditions Observed: No Food Safety Manager on site. Train an employee and keep cert onsite. This employee will be responsible for communicating this food safety knowledge to all food handlers. Correct within 60 days to avoid reinspection fees.
ROACHY SAYS:
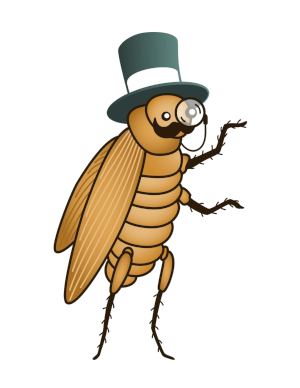
“The Person In Charge (PIC) and all employees shall have adequate knowledge and shall be properly trained in food safety as it relates to their assigned duties. The PIC shall have adequate knowledge of major food allergens, foods identified as major food allergens, and the symptoms that a major food allergen could cause. The PIC means a designated person who has knowledge of safe food handling practices and the major food allergens as they relate to the specific food preparation activities that occur at the food facility. (113947)”
02. Food safety certification, food handler card compliance
Conditions Observed: No current food handler cards are onsite today. Have all food handlers trained and cert copies kept onsite. Correct within 30 days to avoid reinspection fees.
ROACHY SAYS:
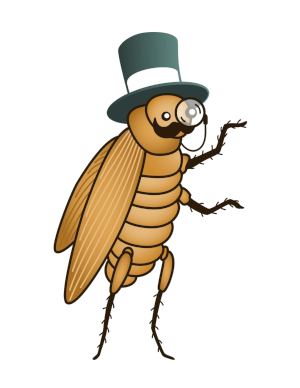
“Food facilities that prepare, handle, or serve non-prepackaged potentially hazardous food, shall have an owner or employee who has passed an aproved food safety certification examination. Food handlers that prepare, handle, or serve non-prepackaged potentially hazardous food, shall obtain a valid Food Handler Card within 30 days after date of hire. (113947.1-113947.5, 113948)”
06. Hands clean and properly washed; gloves used properly.
Conditions Observed: Observed food handler pick up raw beef steak place onto grill before handling ready to eat toast. Food handler was immediately notified to discard toast, wash hands and change gloves. Train all food handlers in proper handwashing and glove use. Hands must be washed prior to glove don and change.
ROACHY SAYS:
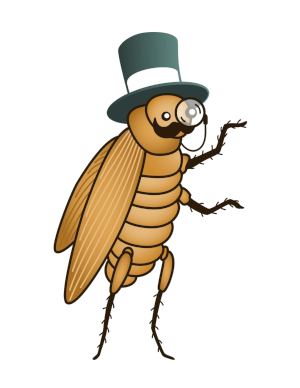
“Food employees shall minimize bare hand and arm contact with nonprepackaged food that is in ready to eat form. Whenever gloves are worn, they shall be changed, replaced, or washed as often as handwashing is required. Single-use gloves shall not be washed. Employees shall wash their hands in the following situations: immediately before engaging in food preparation including working with nonprepackaged food, clean equipment and utensils and unwrapped single-use food containers and utensils; after touching bare human body parts other than clean hands and clean exposed portions of arms; after using the toilet room; after caring for or handling any animal; after coughing, sneezing, using a handkerchief or disposable tissue, using tobacco, eating or drinking; after handling soiled equipment or utensils; during food preparation, as often as necessary to remove soil and contamination and to prevent cross-contamination when changing tasks; when switching from working with raw food and working with ready-to-eat foods; before initially donning gloves for working with food; before dispensing or serving food handling clean tableware and serving utensils in the food service area; after engaging in other activities that contaminate the hands. (113952, 113953.3, 113953.4, 113961, 113968, 113973)”
07. Adequate handwash facilities supplied and accessible.
Conditions Observed: 2 compartment sink that doubles as prep, warewash, and handwashing was blocked by dirty dishes and had no handsoap. With this as well as the handwashing deficiencies taken into account, the facility must add a dedicated handwashing sink to the prep area by the date noted.
ROACHY SAYS:
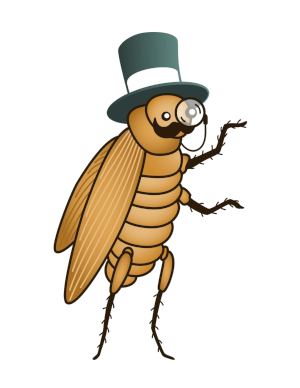
“Handwashing facilities shall be provided within or adjacent to toilet rooms, food preparation, and warewashing areas. Handwashing facilities shall be clean, unobstructed, and accessible at all times. Handwashing facilities shall be provided with soap and sanitary single use towels in approved dispensers. Dispensers shall be maintained in good repair. A handwashing facility shall not be used for purposes other than handwashing. (113953, 113953.1, 113953.2, 114067(f))”
08. Proper hot and cold holding temperatures.
Conditions Observed: The cold hold unit adjacent to the cookline was not operable. Foods held on ice which had melted leaving foods ranging from 43 to 50F. One item was discarded and ice added to bottom of unit. This unit was not designed as an ice back and must be repaired or replaced by 12/14/19 to avoid reinspection fees. In meantime, foods kept at or below 41F. This can be achieved short term with monitoring of the ice bath.
ROACHY SAYS:
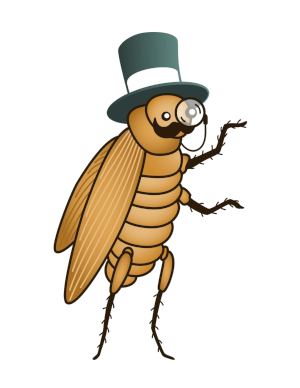
“Except during preparation, cooking, cooling, transportation to or from a retail food facility for a period of less than thirty minutes, when time is used as the public health control, or as otherwise specified, potentially hazardous foods shall be maintained at or below 41F or at or above 135F. The following foods may be held at or below 45F: raw shell eggs, unshucked live molluscan shellfish, pasteurized milk and pasteurized milk products in original sealed containers, potentially hazardous foods held during transportation. Potentially hazardous foods held for dispensing in serving lines and salad bars may be held at 45F, not to exceed 12 hours in a 24 hour period, if unused portions are discarded. Food preparation shall not exceed two cumulative hours without a return to the required holding temperatures. (113996, 113998, 114037, 114343(a))”
09. Time as public health control; procedures and records.
Conditions Observed: TPHC procedure was not being followed. Shell eggs, uncooked cut potatoes, batters were found out, without disposal time labeled. Foods were discarded. Facility must adhere to this procedure or it will be revoked and foods held under refrigeration.
ROACHY SAYS:
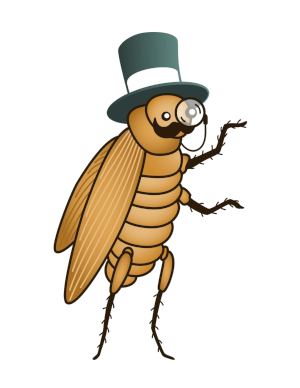
“When time as a public health control is used, the following procedures shall be observed: food items shall be marked to indicate four hours past the time when the food was removed from temperature control, food shall be served or discarded within the four hour time limit. Written procedures shall be maintained in the food facility and made available to the enforcement agency upon request, that ensure compliance with this section and section 114002, for food that is prepared, cooked, and refrigerated before time is used as a public health control. Time only may not be used in Licensed health care facilities, public school cafeterias, or private school cafeterias. (114000)”
10. Proper cooling methods.
Conditions Observed: Cooked gravy was observed cooling on a countertop in a narrow plastic bin. This in not an approved active cooling method. Approved cooling methods include ice paddles, ice baths, cooling in shallow pans or added ice to food. Develop an effective procedure to adequately cool these foods. Food was reheated and approved method of cooling attempted. If this food does not meet cooling reqs, discard.
ROACHY SAYS:
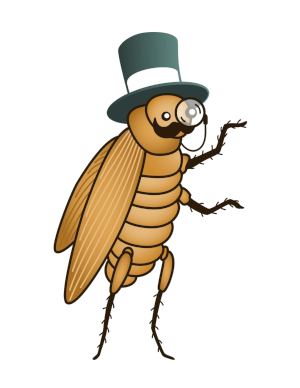
“After heating, potentially hazardous foods shall be rapidly cooled from 135F to 70F within 2 hours, and then from 70F to 41F within 4 hours. Potentially hazardous foods prepared from ambient temperature ingredients must be cooled to below 41F within 4 hours. Cooling shall be facilitated by one or more of the following methods: in shallow pans, separating food into smaller portions, adding ice as an ingredient, using an ice bath and stirring frequently, using an ice paddle, using rapid cooling equipment, or using containers that facilitate heat transfer. (114002, 114002.1)”
44. Premises; personal/cleaning items; vermin-proofing.
Conditions Observed: There is a large chewed hole around the rear storage shed door threshhold. While no other rodent sign was noted, this is evidence of past activity as well as a potential future ingress point. Repair this damage.
ROACHY SAYS:
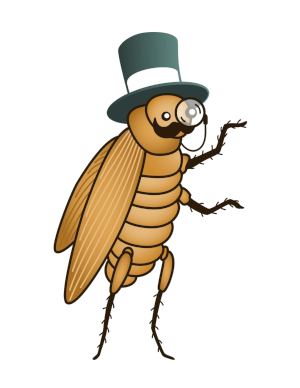
“All premises of a food facility shall be kept clean, fully operative, and in good repair. The premise of a food facility shall be free of litter and items unnecessary to the operation of the facility. Areas designated for employees to eat and drink shall be located so that food, clean equipent and utensils, linens, and single-use articles are protected from contamination. Personal items shall be stored in a designated area to prevent contamination of food or utensils. Food prep sinks, warewashing sinks, and handwashing sinks shall not be used for the cleaning or maintenance of tools or cleaning supplies or to dispose of mop water and similar liquid wastes. A dedicated janitorial sink with a drain shall be provided and conveniently located. A separate room, area, or cabinet shall be provided for cleaning supplies. The facility shall be kept vermin proof. Insect electrocution devices shall retain the insect within the device and shall not be located over food or utensil handling areas. (114123, 114143(a, b), 114256, 114256.1, 114256.2, 114256.4, 114257, 114257.1, 114259, 114259.2, 114259.3, 114279, 114281, 114282)”
45. Floor, walls, and ceilings: built, maintained, clean.
Conditions Observed: Floors have not been replaced as agreed to in compliance schedule dated 1/18/19. An extension is granted to make the floors smooth, easily cleanable and clean. After this date , facility will be billed at the hourly rate for time spent gaining compliance, including reinspections and office time.
ROACHY SAYS:
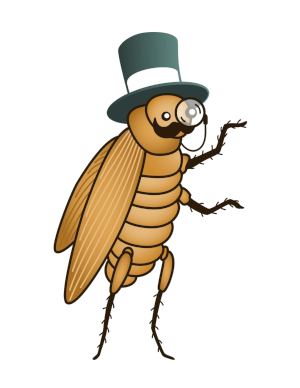
“Food facilities shall be fully enclosed in a building consisting of permanent floors, walls, and an overhead structure that meets minimum standards. The walls and ceiling shall be smooth, durable, nonabsorbent, and easily cleanable. Flooring and base coving shall be smooth, durable, and made of approved nonabsorbent material that is easily cleanable. Floor surfaces shall be coved at the juncture of the floor and wall with a 3/8 inch minimum radius and shall extend up the wall at least 4 inches. (114143(d), 114266, 114268, 114268.1, 114271, 114272)”