Westside Pizza
600 F St 1 Ste, Arcata
Monday, Nov. 8, 2021 (1 violation)
Routine Inspection
08. Proper hot and cold holding temperatures.
ROACHY SAYS:
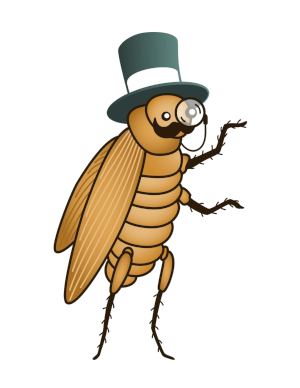
“Except during preparation, cooking, cooling, transportation to or from a retail food facility for a period of less than thirty minutes, when time is used as the public health control, or as otherwise specified, potentially hazardous foods shall be maintained at or below 41F or at or above 135F. The following foods may be held at or below 45F: raw shell eggs, unshucked live molluscan shellfish, pasteurized milk and pasteurized milk products in original sealed containers, potentially hazardous foods held during transportation. Potentially hazardous foods held for dispensing in serving lines and salad bars may be held at 45F, not to exceed 12 hours in a 24 hour period, if unused portions are discarded. Food preparation shall not exceed two cumulative hours without a return to the required holding temperatures. (113996, 113998, 114037, 114343(a))”
Wednesday, July 14, 2021 (1 violation)
Routine Inspection
09. Time as public health control; procedures and records.
Conditions Observed: Facility lacks a written procedure and time marking for pizza offered by the slice. As discussed during the inspection, develop a written procedure for pizza held using Time as Public Health Control. Label pizzas with the time that indicates four hours from when pizzas were removed from the oven.
ROACHY SAYS:
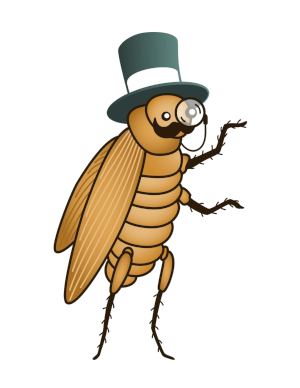
“When time as a public health control is used, the following procedures shall be observed: food items shall be marked to indicate four hours past the time when the food was removed from temperature control, food shall be served or discarded within the four hour time limit. Written procedures shall be maintained in the food facility and made available to the enforcement agency upon request, that ensure compliance with this section and section 114002, for food that is prepared, cooked, and refrigerated before time is used as a public health control. Time only may not be used in Licensed health care facilities, public school cafeterias, or private school cafeterias. (114000)”
Monday, March 1, 2021 (0 violations)
Routine Inspection
ROACHY SAYS:
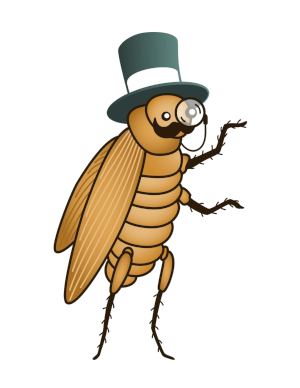
“Ooo! Welcome to Sanitarytown! Population: Westside Pizza! I see lots of happy hungry mouths in this establishment's near future!!”
Thursday, Oct. 15, 2020 (0 violations)
Routine Inspection
ROACHY SAYS:
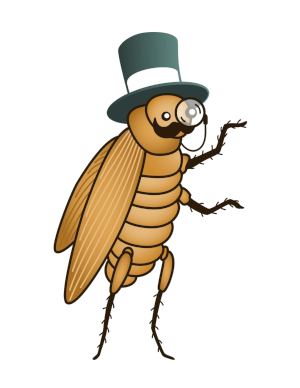
“Both patrons and the health department agree! This place sets the standard for Humboldt food facility cleanliness! All hail Westside Pizza!!”
Wednesday, June 10, 2020 (2 violations)
Routine Inspection
15. Food contact surfaces: clean and sanitized.
Conditions Observed: Measured chlorine in the sanitizing bin to be less than 100 PPM. Discussed bleach and measuring with test strips. Operator drained and will refill when next batch of utensils are ready to be washed - COS.
ROACHY SAYS:
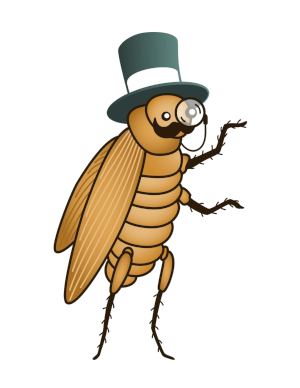
“Food-contact surfaces and utensils shall be clean to sight and touch. Food-contact surfaces and multiservice utensils shall be effectively washed, rinsed, and sanitized to remove or completely loosen soils by use of manual or mechanical methods. Precleaning may be required. Manual sanitization shall be accomplished during the final rinse by contact with solution containing 100 ppm available chlorine, 200 ppm quaternary ammonium, or another approved sanitizer. Mechanical sanitization shall be accomplished in the final rinse by achieving a utensil surface temperature of 160F or by contact with solution containing 50 ppm available chlorine, 200 ppm quaternary ammonium, or another approved sanitizer. After cleaning and sanitizing, equipment and utensils shall be air dried. Mechancial warewash machines must be approved and installed and operated according to manufacturer's specifications. Food contact surfaces, utensils, and equipment shall be cleaned and sanitized at the following times: before each use with different type of raw food of animal origin, when changing from raw food to ready to eat food, between uses with raw produce and potentially hazardous food, before using a thermometer, and any time during the operation when contamination may have occurred. Warewash sinks used to wash wiping cloths, wash produce, or thaw food must be cleaned and sanitized before and after these uses. Equipment, food contact surfaces, and utensils must be cleaned and sanitized throughout the day at least every four hours or as needed to prevent contamination. (114097, 114099.1, 114099.2, 114099.4, 114099.6, 114099.7, 114101, 114105, 114109, 114111, 114113, 114115(a,c), 114117, 114125(b), 114141)”
36. Equipment / Utensils approved; installed, clean, good repair, capacity.
Conditions Observed: Observed the use of paint brushes to add butter to crusts. Bristles appear to be a hair-like material that may be difficult to effectively sanitize. Replace with a brush intended for use with foods and can be washed, rinsed, and sanitized. Owner ordered conforming brushes during the Inspection - COS.
ROACHY SAYS:
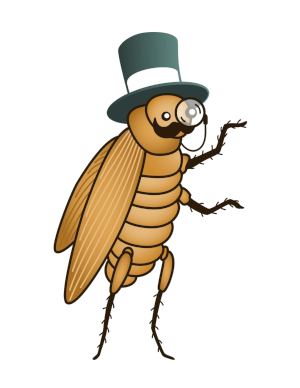
“Utensils and equipment shall be kept fully operative and in good repair. All new and replacement equipment shall be properly installed and be certified or classified for sanitation by an ANSI accredited certification program. Electrical appliances must meet UL standards. Single-use articles shall not allow migration of deleterious substances or impart colors, odors, or tastes to food. Multi-use food contact surfaces must be smooth, free of breaks, chips, and similar imperfections; free of sharp internal angles, corners, and crevices; finished to have smooth welds and joints; be accessible for cleaning and inspection. Unless specified, wood and wood wicker may not be used as a food-contact surface. Unless specified, copper and copper alloys such as brass may not be used in contact with a food that has a pH below six or for a fitting between a backflow preventer and a carbonator. Beverage tubing and cold-plate beverage cooling devices cannot be installed in contact with stored ice intended to be used as food. Equipment that is not movable must be installed to allow for cleaning in place. Cutting or piercing parts of can openers must be readily removable. Facilities that wash, rinse, soak, thaw, or similarly prepare foods shall be provided with a approved food preparation sink. Reservoirs that supply water to produce foggers must be cleaned and maintained. Surfaces such as cutting blocks and boards that are subject to scratching and scoring shall be resurfaced or replaced if they can no longer be effectively cleaned and sanitized. (114130, 114130.1, 114130.2, 114130.3, 114130.4, 114130.5, 114130.6, 114132, 114133, 114137, 114139, 114153, 114163, 114165, 114167, 114169, 114175, 114177, 114180, 114182)”
Friday, Jan. 3, 2020 (3 violations)
CP - Change of Ownership
34. Non-food-contact surfaces clean.
Conditions Observed: Observed build-up on holster for table-mounted can opener; observed minor debris on can opener. Observed minor black, mildew-like buildup on side of ice dispenser (showed observations to Owner). Clean and sanitize routinely to avoid build-up.
ROACHY SAYS:
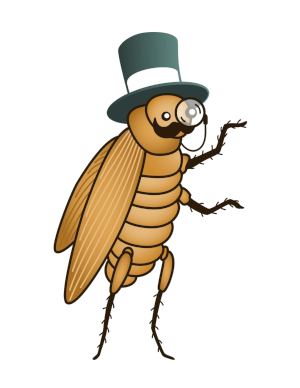
“Nonfood-contact surfaces of equipment shall be kept free of an accumulation of dust, dirt, food residue, and other debris. (114115(b))”
37. Equipment, utensils and linens: storage and use.
Conditions Observed: Observed paint bucket used to flour resting on top of bulk flour. Keep bucket separate from floor. Owner brought bucket to 3-part sink. COS.
ROACHY SAYS:
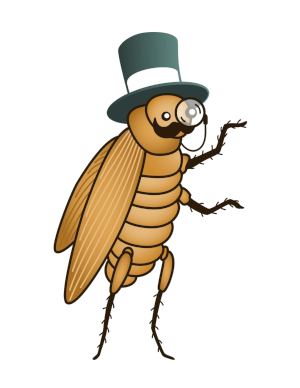
“Clean equipment, utensils, linens, and single-use articles shall be stored at least six inches above the floor in an approved location within the fully enclosed permitted food facility. Clean equipment, utensils, linens, and single-use articles shall not be exposed to splash, dust, vermin, or other forms of contamination. Non-food items shall be stored and displayed separate from food and food-contact surfaces. During pauses in food preparation utensils shall be stored with handles above the top of the food, on a clean sanitized surface, in running water, or in water that is at least 135øF. Single-use articles and multiservice utensils shall be handled, displayed, and dispensed so that contamination of food and lip-contact surfaces is prevented. Extra preset tableware shall be removed when a consumer is seated or cleaned and sanitized before further use. Pressurized cylinders shall be securely fastened to rigid structure. Linens must be free of food residue and soil and be laundered as required. (114074, 114075(a,b,d,e), 114081, 114119, 114121, 114161, 114172, 114178, 114179, 114083, 114185, 114185.2, 114185.3, 114185.4, 114185.5)”
39. Thermometers provided and accurate.
Conditions Observed: No thermometer in the short deli prep. Owner provided a thermometer - COS. Be sure all units have an adequate NSF approved thermometer.
ROACHY SAYS:
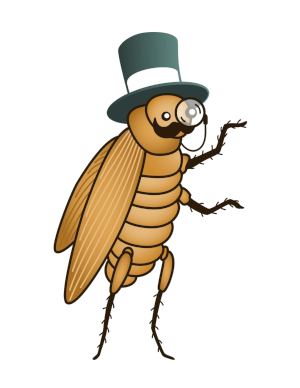
“An accurate easily readable metal probe thermometer suitable for measuring temperature of food shall be available to the food handler. Thermometers shall be calibrated in accordance with manufacturer's specifications as necessary to ensure their accuracy. A thermometer +/- 2 degrees F shall be provided for all refrigerators, hot and cold holding units, and high temperature warewashing machines. (114157, 114159)”
Thursday, Nov. 14, 2019 (6 violations)
Routine Inspection
07. Adequate handwash facilities supplied and accessible.
Conditions Observed: Observed trays, a cart, and crates partially obstructing handwashing sink in dough room. Observed container of bulk soap in handwashing sink. Keep handwashing sink empty and unobstructed at all times for frequent and hygienic handwashing.
ROACHY SAYS:
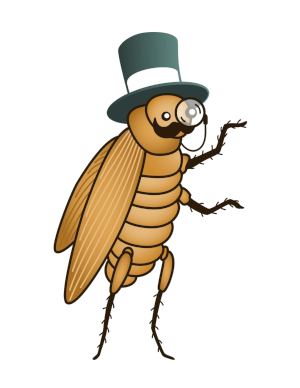
“Handwashing facilities shall be provided within or adjacent to toilet rooms, food preparation, and warewashing areas. Handwashing facilities shall be clean, unobstructed, and accessible at all times. Handwashing facilities shall be provided with soap and sanitary single use towels in approved dispensers. Dispensers shall be maintained in good repair. A handwashing facility shall not be used for purposes other than handwashing. (113953, 113953.1, 113953.2, 114067(f))”
15. Food contact surfaces: clean and sanitized.
Conditions Observed: Initially measured 0 PPM QT sanitizer in third bin at 3-part sink. Operator dispensed QT into small container, measured QT to be 100 PPM. No sanitizer in red sani-bucket at pizza counter. Reviewed approved sanitizers/effective sanitizing with PIC. Use 1 tablespoon of bleach per 1 gallon of cool water to make a 100 PPM chorine solution. Allow dishes to soak for at least 30 seconds. Operator obtained bleach and filled the sanitizing bin/bucket. Measured chlorine to be 100PPM. COS. If you choose to use the wall mounted system, adjust/service/repair to deliver QT at 200 PPM. Never mix sanitizers. Observed build-up on triangular prong on table mounted can opener. Remove build-up; clean and sanitize.
ROACHY SAYS:
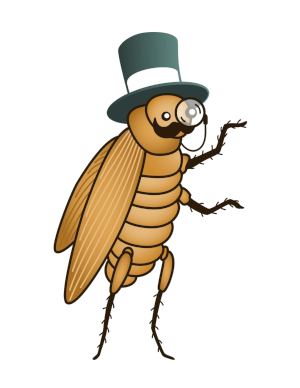
“Food-contact surfaces and utensils shall be clean to sight and touch. Food-contact surfaces and multiservice utensils shall be effectively washed, rinsed, and sanitized to remove or completely loosen soils by use of manual or mechanical methods. Precleaning may be required. Manual sanitization shall be accomplished during the final rinse by contact with solution containing 100 ppm available chlorine, 200 ppm quaternary ammonium, or another approved sanitizer. Mechanical sanitization shall be accomplished in the final rinse by achieving a utensil surface temperature of 160F or by contact with solution containing 50 ppm available chlorine, 200 ppm quaternary ammonium, or another approved sanitizer. After cleaning and sanitizing, equipment and utensils shall be air dried. Mechancial warewash machines must be approved and installed and operated according to manufacturer's specifications. Food contact surfaces, utensils, and equipment shall be cleaned and sanitized at the following times: before each use with different type of raw food of animal origin, when changing from raw food to ready to eat food, between uses with raw produce and potentially hazardous food, before using a thermometer, and any time during the operation when contamination may have occurred. Warewash sinks used to wash wiping cloths, wash produce, or thaw food must be cleaned and sanitized before and after these uses. Equipment, food contact surfaces, and utensils must be cleaned and sanitized throughout the day at least every four hours or as needed to prevent contamination. (114097, 114099.1, 114099.2, 114099.4, 114099.6, 114099.7, 114101, 114105, 114109, 114111, 114113, 114115(a,c), 114117, 114125(b), 114141)”
22. Hot and Cold Water Available
Conditions Observed: Warm water faucet at dough room handwash is non-operational. Repair to deliver warm water at 100 to 108 F.
ROACHY SAYS:
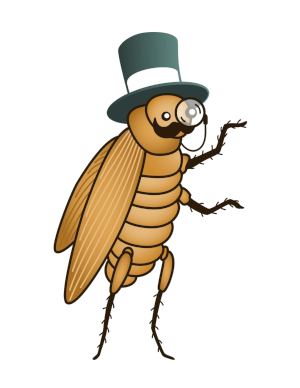
“An adequate, protected, pressurized, approved potable supply of hot and cold water shall be provided at all times. Hot water shall be supplied at a minimum temperature of 120F when measured from the faucet. The temperature of water provided to handwashing facilities shall be at least 100F. Handwashing facilities equipped with non-adjustable faucets shall have their temperature set between 100F and 108F. Hot water shall be provided at the food preparation sink and janitorial sink. (113953(c), 114099.2(b), 114163(a)(3), 114189, 114192, 114192.1, 114195)”
34. Non-food-contact surfaces clean.
Conditions Observed: Observed build-up in floor sink below prep sink. Remove build-up; clean and sanitize.
ROACHY SAYS:
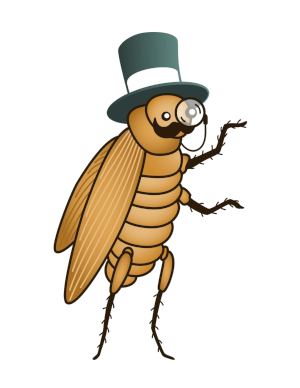
“Nonfood-contact surfaces of equipment shall be kept free of an accumulation of dust, dirt, food residue, and other debris. (114115(b))”
35. Warewashing: installed, maintained, used, Adequate Means to measure sanitizer
Conditions Observed: No test strips available for QT sanitizer (the sanitizer in use at the time of inspection). Obtain the appropriate test strips. Use each time you make a sanitizing solution. Provided PIC with a strip of chlorine (white) and QT (orange) test strips.
ROACHY SAYS:
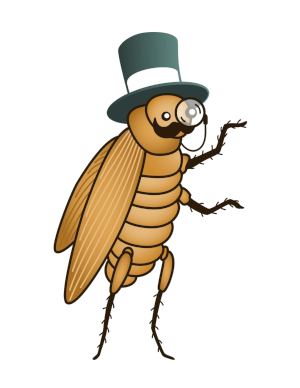
“Facilities that prepare food shall be equipped with a manual warewashing sink that has at least three compartments with two integral metal drainboards, except as specified in 114099(c). A warewashing sink shall not be used for handwashing except as specified in 114125(a). Sink compartments shall be large enough to accommodate immersion of the largest equipment and utensils used. Testing materials shall be provided to adequately measure the applicable sanitization method used during manual or mechanical warewashing. (114067(f,g), 114099, 114099.3, 114099.5, 114101(a), 114101.1, 114101.2, 114103, 114107, 114125(a))”
39. Thermometers provided and accurate.
Conditions Observed: No thermometer in 2-door prep fridge. Provide a thermometer for this unit.
ROACHY SAYS:
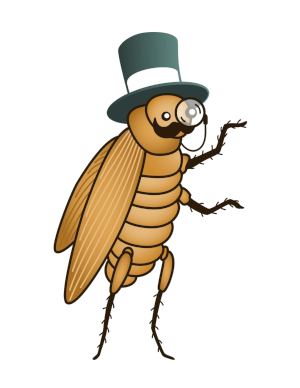
“An accurate easily readable metal probe thermometer suitable for measuring temperature of food shall be available to the food handler. Thermometers shall be calibrated in accordance with manufacturer's specifications as necessary to ensure their accuracy. A thermometer +/- 2 degrees F shall be provided for all refrigerators, hot and cold holding units, and high temperature warewashing machines. (114157, 114159)”
Wednesday, June 19, 2019 (4 violations)
Routine Inspection
07. Adequate handwash facilities supplied and accessible.
Conditions Observed: Observed milk crates and trash bin obstructing handwashing sink in dough room. Keep sink unobstructed and accessible at all times.
ROACHY SAYS:
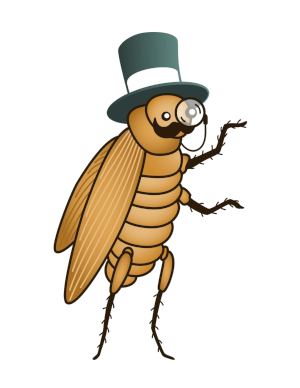
“Handwashing facilities shall be provided within or adjacent to toilet rooms, food preparation, and warewashing areas. Handwashing facilities shall be clean, unobstructed, and accessible at all times. Handwashing facilities shall be provided with soap and sanitary single use towels in approved dispensers. Dispensers shall be maintained in good repair. A handwashing facility shall not be used for purposes other than handwashing. (113953, 113953.1, 113953.2, 114067(f))”
36. Equipment / Utensils approved; installed, clean, good repair, capacity.
Conditions Observed: Handle for walkin has failed. Replace or properly repair to be operative and in good condition. Please correct prior to the next routine inspection.
ROACHY SAYS:
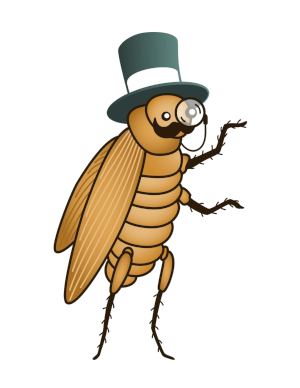
“Utensils and equipment shall be kept fully operative and in good repair. All new and replacement equipment shall be properly installed and be certified or classified for sanitation by an ANSI accredited certification program. Electrical appliances must meet UL standards. Single-use articles shall not allow migration of deleterious substances or impart colors, odors, or tastes to food. Multi-use food contact surfaces must be smooth, free of breaks, chips, and similar imperfections; free of sharp internal angles, corners, and crevices; finished to have smooth welds and joints; be accessible for cleaning and inspection. Unless specified, wood and wood wicker may not be used as a food-contact surface. Unless specified, copper and copper alloys such as brass may not be used in contact with a food that has a pH below six or for a fitting between a backflow preventer and a carbonator. Beverage tubing and cold-plate beverage cooling devices cannot be installed in contact with stored ice intended to be used as food. Equipment that is not movable must be installed to allow for cleaning in place. Cutting or piercing parts of can openers must be readily removable. Facilities that wash, rinse, soak, thaw, or similarly prepare foods shall be provided with a approved food preparation sink. Reservoirs that supply water to produce foggers must be cleaned and maintained. Surfaces such as cutting blocks and boards that are subject to scratching and scoring shall be resurfaced or replaced if they can no longer be effectively cleaned and sanitized. (114130, 114130.1, 114130.2, 114130.3, 114130.4, 114130.5, 114130.6, 114132, 114133, 114137, 114139, 114153, 114163, 114165, 114167, 114169, 114175, 114177, 114180, 114182)”
44. Premises; personal/cleaning items; vermin-proofing.
Conditions Observed: Observed light leaks at bottom corners of back door - repair door to be vermin proof. Door to dough room was open today. Keep door closed to maintain a vermin proof facility.
ROACHY SAYS:
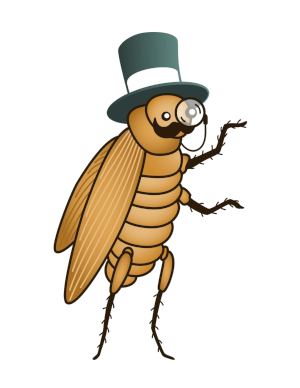
“All premises of a food facility shall be kept clean, fully operative, and in good repair. The premise of a food facility shall be free of litter and items unnecessary to the operation of the facility. Areas designated for employees to eat and drink shall be located so that food, clean equipent and utensils, linens, and single-use articles are protected from contamination. Personal items shall be stored in a designated area to prevent contamination of food or utensils. Food prep sinks, warewashing sinks, and handwashing sinks shall not be used for the cleaning or maintenance of tools or cleaning supplies or to dispose of mop water and similar liquid wastes. A dedicated janitorial sink with a drain shall be provided and conveniently located. A separate room, area, or cabinet shall be provided for cleaning supplies. The facility shall be kept vermin proof. Insect electrocution devices shall retain the insect within the device and shall not be located over food or utensil handling areas. (114123, 114143(a, b), 114256, 114256.1, 114256.2, 114256.4, 114257, 114257.1, 114259, 114259.2, 114259.3, 114279, 114281, 114282)”
45. Floor, walls, and ceilings: built, maintained, clean.
Conditions Observed: Flooring/coving has failed to the right of the 3-part sink. Repair surfaces to be smooth, durable, and easily cleanable and to eliminate vermin attraction/harborage.
ROACHY SAYS:
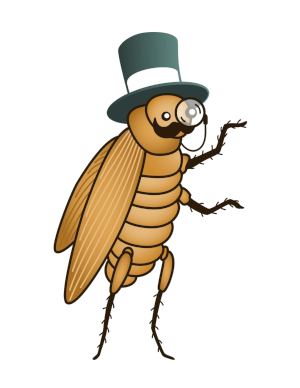
“Food facilities shall be fully enclosed in a building consisting of permanent floors, walls, and an overhead structure that meets minimum standards. The walls and ceiling shall be smooth, durable, nonabsorbent, and easily cleanable. Flooring and base coving shall be smooth, durable, and made of approved nonabsorbent material that is easily cleanable. Floor surfaces shall be coved at the juncture of the floor and wall with a 3/8 inch minimum radius and shall extend up the wall at least 4 inches. (114143(d), 114266, 114268, 114268.1, 114271, 114272)”
Friday, Feb. 8, 2019 (5 violations)
Routine Inspection
15. Food contact surfaces: clean and sanitized.
Conditions Observed: Observed build-up on table mounted can opener and holster. Remove build-up; clean and sanitize.
ROACHY SAYS:
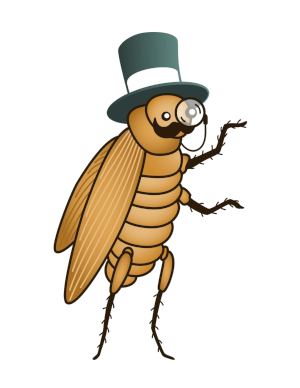
“Food-contact surfaces and utensils shall be clean to sight and touch. Food-contact surfaces and multiservice utensils shall be effectively washed, rinsed, and sanitized to remove or completely loosen soils by use of manual or mechanical methods. Precleaning may be required. Manual sanitization shall be accomplished during the final rinse by contact with solution containing 100 ppm available chlorine, 200 ppm quaternary ammonium, or another approved sanitizer. Mechanical sanitization shall be accomplished in the final rinse by achieving a utensil surface temperature of 160F or by contact with solution containing 50 ppm available chlorine, 200 ppm quaternary ammonium, or another approved sanitizer. After cleaning and sanitizing, equipment and utensils shall be air dried. Mechancial warewash machines must be approved and installed and operated according to manufacturer's specifications. Food contact surfaces, utensils, and equipment shall be cleaned and sanitized at the following times: before each use with different type of raw food of animal origin, when changing from raw food to ready to eat food, between uses with raw produce and potentially hazardous food, before using a thermometer, and any time during the operation when contamination may have occurred. Warewash sinks used to wash wiping cloths, wash produce, or thaw food must be cleaned and sanitized before and after these uses. Equipment, food contact surfaces, and utensils must be cleaned and sanitized throughout the day at least every four hours or as needed to prevent contamination. (114097, 114099.1, 114099.2, 114099.4, 114099.6, 114099.7, 114101, 114105, 114109, 114111, 114113, 114115(a,c), 114117, 114125(b), 114141)”
34. Non-food-contact surfaces clean.
Conditions Observed: Observed excessive food debris on the side of the small deli prep. Remove debris. Clean and sanitize.
ROACHY SAYS:
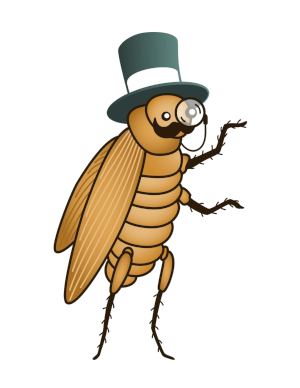
“Nonfood-contact surfaces of equipment shall be kept free of an accumulation of dust, dirt, food residue, and other debris. (114115(b))”
36. Equipment / Utensils approved; installed, clean, good repair, capacity.
Conditions Observed: Handle on walkin has failed. Replace with a proper handle. This is a repeat violation.
ROACHY SAYS:
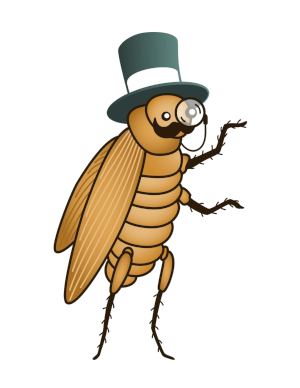
“Utensils and equipment shall be kept fully operative and in good repair. All new and replacement equipment shall be properly installed and be certified or classified for sanitation by an ANSI accredited certification program. Electrical appliances must meet UL standards. Single-use articles shall not allow migration of deleterious substances or impart colors, odors, or tastes to food. Multi-use food contact surfaces must be smooth, free of breaks, chips, and similar imperfections; free of sharp internal angles, corners, and crevices; finished to have smooth welds and joints; be accessible for cleaning and inspection. Unless specified, wood and wood wicker may not be used as a food-contact surface. Unless specified, copper and copper alloys such as brass may not be used in contact with a food that has a pH below six or for a fitting between a backflow preventer and a carbonator. Beverage tubing and cold-plate beverage cooling devices cannot be installed in contact with stored ice intended to be used as food. Equipment that is not movable must be installed to allow for cleaning in place. Cutting or piercing parts of can openers must be readily removable. Facilities that wash, rinse, soak, thaw, or similarly prepare foods shall be provided with a approved food preparation sink. Reservoirs that supply water to produce foggers must be cleaned and maintained. Surfaces such as cutting blocks and boards that are subject to scratching and scoring shall be resurfaced or replaced if they can no longer be effectively cleaned and sanitized. (114130, 114130.1, 114130.2, 114130.3, 114130.4, 114130.5, 114130.6, 114132, 114133, 114137, 114139, 114153, 114163, 114165, 114167, 114169, 114175, 114177, 114180, 114182)”
44. Premises; personal/cleaning items; vermin-proofing.
Conditions Observed: Observed light leaks at the bottom corner of the back door. Repair door to be flush with floor, tightly fitting, and vermin proof.
ROACHY SAYS:
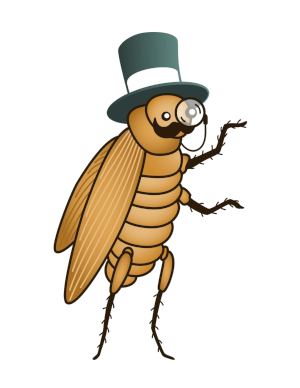
“All premises of a food facility shall be kept clean, fully operative, and in good repair. The premise of a food facility shall be free of litter and items unnecessary to the operation of the facility. Areas designated for employees to eat and drink shall be located so that food, clean equipent and utensils, linens, and single-use articles are protected from contamination. Personal items shall be stored in a designated area to prevent contamination of food or utensils. Food prep sinks, warewashing sinks, and handwashing sinks shall not be used for the cleaning or maintenance of tools or cleaning supplies or to dispose of mop water and similar liquid wastes. A dedicated janitorial sink with a drain shall be provided and conveniently located. A separate room, area, or cabinet shall be provided for cleaning supplies. The facility shall be kept vermin proof. Insect electrocution devices shall retain the insect within the device and shall not be located over food or utensil handling areas. (114123, 114143(a, b), 114256, 114256.1, 114256.2, 114256.4, 114257, 114257.1, 114259, 114259.2, 114259.3, 114279, 114281, 114282)”
45. Floor, walls, and ceilings: built, maintained, clean.
Conditions Observed: Observed floor to have failed at the 3-part sink. Observed gaps in finish on wall between dough room and counter. Repair/replace so that floors and all finishes are smooth, durable, non-absorbent and free of harborage.
ROACHY SAYS:
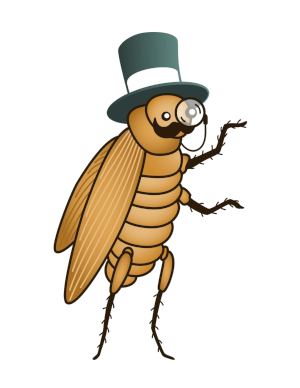
“Food facilities shall be fully enclosed in a building consisting of permanent floors, walls, and an overhead structure that meets minimum standards. The walls and ceiling shall be smooth, durable, nonabsorbent, and easily cleanable. Flooring and base coving shall be smooth, durable, and made of approved nonabsorbent material that is easily cleanable. Floor surfaces shall be coved at the juncture of the floor and wall with a 3/8 inch minimum radius and shall extend up the wall at least 4 inches. (114143(d), 114266, 114268, 114268.1, 114271, 114272)”