[Ed. note — Author Gillen Martin is a Lead for America fellow working out of the City of Arcata. She introduced herself to Outpost readers in this essay.]
###
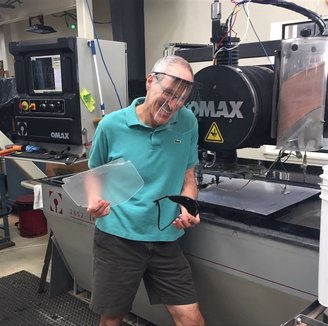
Paul Lubitz of Holly Yashi with one of the face shields his company is now producing.
There is nothing like a pandemic to highlight the correlation between a “go local” culture and community resiliency. As it has become clear that one of the most dangerous and lethal aspects of COVID-19 is its potential to overwhelm healthcare resources, protective gear such as N95 masks, surgical masks, and face shields have become scarce worldwide. In Arcata, however, localized manufacturing is allowing emergency responders to circumnavigate disrupted supply chains and shortages.
Within weeks of closing their Arcata storefront, Creamery District jewelry manufacturer Holly Yashi was producing face shields for emergency responders and public workers. Co-founder Paul Lubitz (“Yashi”) described the time following Humboldt County’s March 19th shelter-in-place order as “exceedingly sad.” Holly Yashi’s Arcata store makes up an impressive 10% of their income worldwide, and production staff that could moved remote while retail staff had to be let go. It is a story familiar around the globe at this point, but no less painful in each instance.
As the business was still adjusting to its new reality in the end of March, Lubitz received a call from his friend José Chavarria––a freelance mechanical design engineer who knew that Holly Yashi uses an OMAX waterjet cutting machine. Chavarria, inspired by the College of the Redwoods’ efforts to 3D-print face shields, made one himself. “It took six hours,” he remembered, “it is awesome that people are making [face shields] with 3D printers, but they are not fast.” Chavarria realized that if a surge in COVID-19 cases produced immediate PPE shortages locally, 3D printing efforts would not be able to scale up enough to meet needs. He also knew that by utilizing Holly Yashi’s waterjet cutter, they would be able to produce up to 1,000 shields per day. “Not many people have a waterjet,” Chavarria said. In fact, Holly Yashi has the only waterjet for hundreds of miles around.
Chavarria called Lubitz to suggest that Holly Yashi start face shield production. Lubitz agreed immediately and sent Chavarria a link to an open source design from Georgia Tech. “That’s the cool thing about Paul,” Chavarria said, “he was just like ‘great, let’s order all of the materials we need.’” For the plastics required, they turned first to Arcata’s CPR Aquatic. There, they found a similar can-do attitude in owner John Nicolini. “It was just a community of local manufacturing people being like ‘whatever’s needed,’” Chavarria recalled, “we can make a lot of stuff here in Arcata.”
Since obtaining materials, Holly Yashi has been producing face shields to stop the spread of the coronavirus in Humboldt County. Due to the critical need, production went from design to finished shields in just a week. “Ingenuity and resourcefulness are some of the traits that Humboldt County is known for, and Holly Yashi’s work further proves why Holly and Paul were recently awarded Business Leaders of the Year,” Executive Director of the Arcata Chamber of Commerce Joellen Clark-Peterson said.
To-date, Lubitz has purchased enough materials to make 600 shields. These are slated to be donated to local emergency responders or purchased at-cost for essential workers. The first order was made by the City of Arcata. “Most of our staff, who work in close proximity to the public, need PPE,” City Engineer Netra Khatri said, “It was perfect timing. We were in immediate need.” Before Khatri ran into Lubitz on his lunch break, the City’s requests from usual suppliers were backordered by weeks. The City also placed an order for 250 face masks from Arcata-based sportswear manufacturer Kokatat.
Localized manufacturing is important to community well-being at all times. A 2015 study by Deloitte found that every manufacturing position creates 2.5 jobs in local goods and services, and for every dollar of value created in manufacturing, another $1.37 is created in additional value in other sectors. Holly Yashi employed 56 people in Arcata, and has managed to keep 29 of those on staff throughout COVID-19 through face shield manufacturing and setting up work-from-home production. Kokatat had 196 employees in their Arcata factory before production closed. However, both of these manufacturers’ efforts during this crisis reflect what Americans seem to be learning repeatedly throughout this pandemic: in the absence of strong federal emergency response, communities step up to serve themselves at local levels.
It is not just Arcata’s larger manufacturers that are supporting local responses to COVID-19. The goodwill, ingenuity, and capacity present in Holly Yashi and Kokatat’s efforts can be found in all sectors of the business community. Arcata Chief of Police Brian Ahearn shared some of the donations that the APD has received: hand sanitizer from Bubbles and Alchemy Distillery, hand-made masks from BigFish Vapor Lab, and food from Café Brio (among others). “It is humbling that the APD was provided all of this with no expectation. Dropped off quietly with no recognition sought…When people give of themselves when they are just as impacted by the crisis as all others, how do you thank them?” Chief Ahearn wondered.
Clark-Peterson suggested thanking Arcata’s businesses by shopping online or leaving positive reviews on social media/websites. As she pointed out, “buying local has taken on a whole new importance in this pandemic.”
COVID-19 is forcing communities to learn and become stronger. Recognizing the importance of buying, manufacturing, and thinking local is not only supporting our response in the short term, but increasing our region’s resiliency for the future.
###
Check out www.visitarcata.com for ways to help local businesses during COVID-19, a directory of Arcata businesses open for business, and more stories and videos of community resiliency.
Information about the City of Arcata’s new Business Resiliency Emergency Loan Program, as well as existing City loan programs, can be found at www.cityofarcata.org.
Holly Yashi has altered the design they are currently using––optimizing for comfort and speed of production––from the original open source Georgia Tech prototype. Anyone with a 3D printer, laser cutter, etc. can access the design at this link.